***I'm wholly unaffiliated with this project***
Driving home over the weekend and saw these condos under construction. Thought the framing was interesting so I stopped for a look.
Any concern with the checks/splits in those cantilevered 4x8s? Or is this already considered in the lumber grading?
Driving home over the weekend and saw these condos under construction. Thought the framing was interesting so I stopped for a look.
Any concern with the checks/splits in those cantilevered 4x8s? Or is this already considered in the lumber grading?
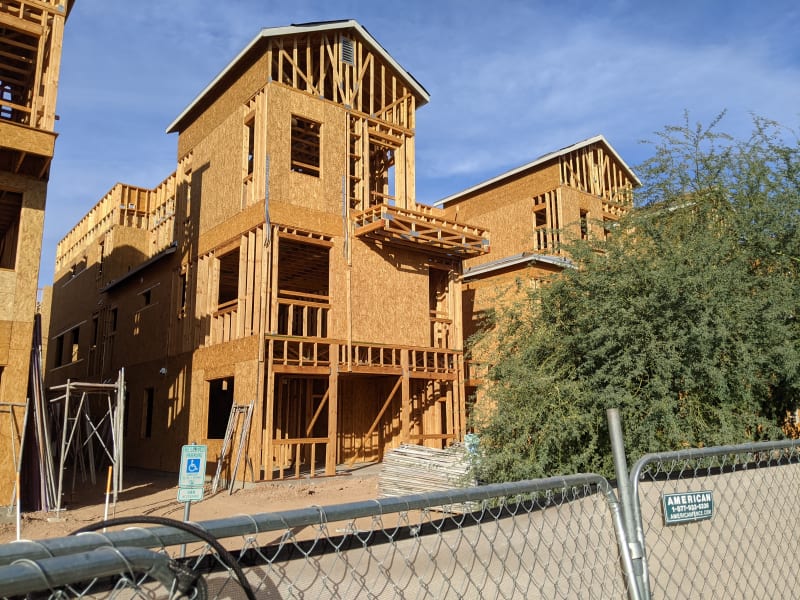
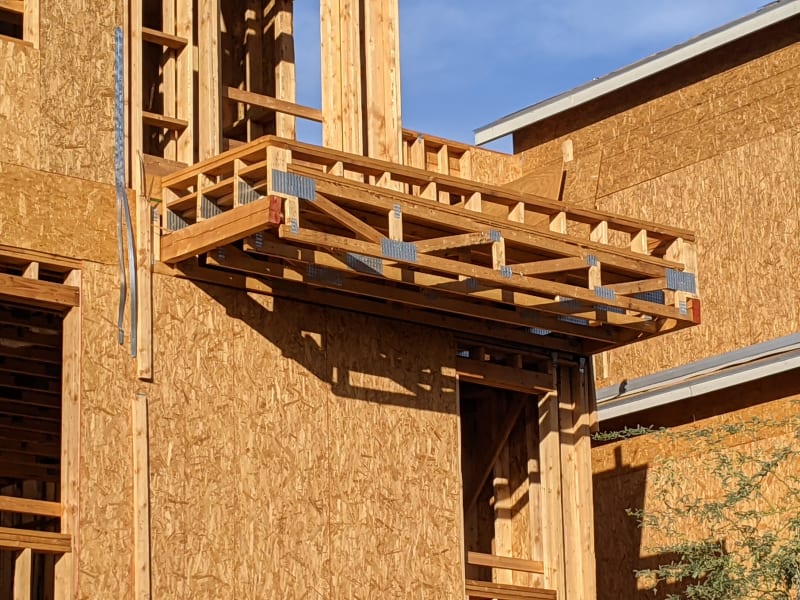
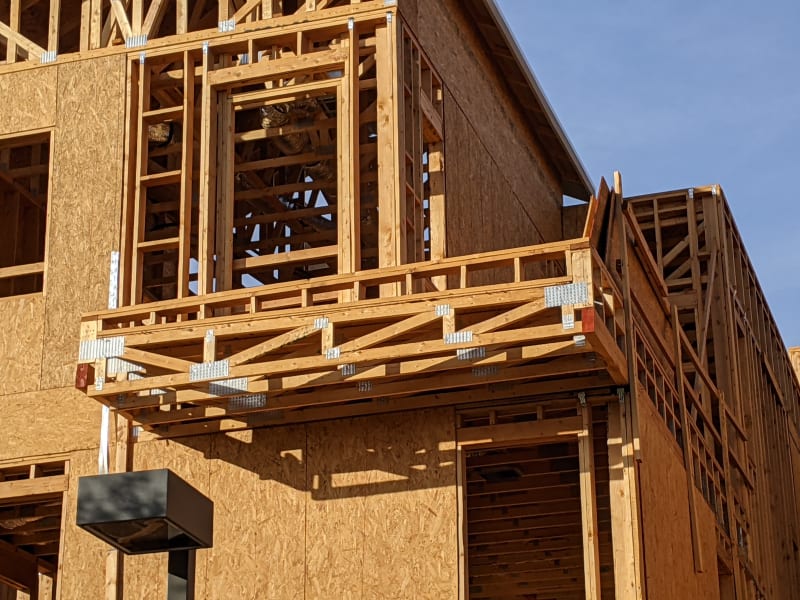
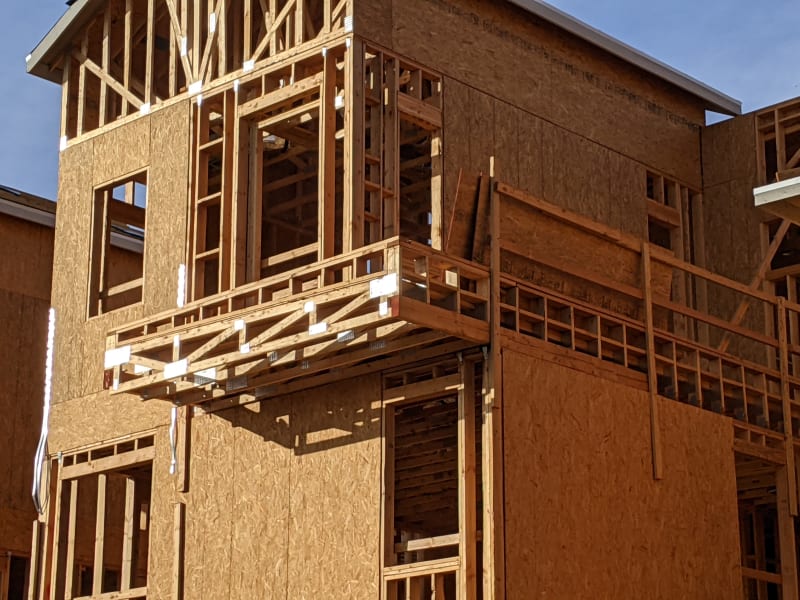