drennon236
Civil/Environmental
I am trying to make a finite element model of a grouted connection with shear keys in monopile:
However, even though I can make a model I am not sure if its correct as I have no experimental data to compare with. I found a paper and design codes online and I am not sure which of these I should compare with (or if there is even any point in comparing the data), and would like to hear a second opinion.
Could I apply a bending moment to my model and check if the maximum nominal radial contact pressure at the top and at the
bottom of the grouted connection is the same as the output from the model? - would this make sense to confirm the accuracy of my model?
Can I use this for comparison - find spring "action force" model and see if its the same as the equation?
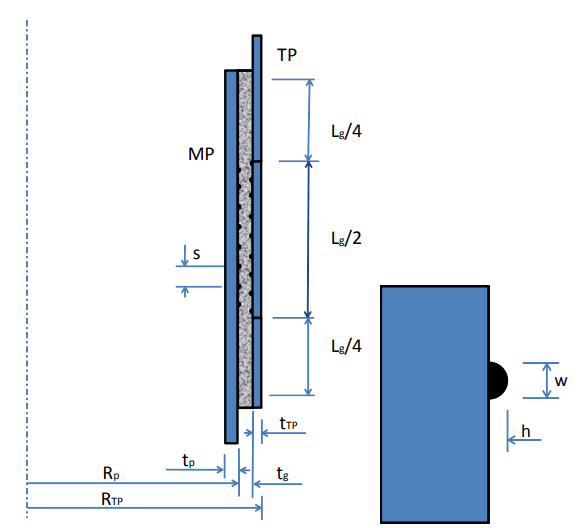
However, even though I can make a model I am not sure if its correct as I have no experimental data to compare with. I found a paper and design codes online and I am not sure which of these I should compare with (or if there is even any point in comparing the data), and would like to hear a second opinion.
Could I apply a bending moment to my model and check if the maximum nominal radial contact pressure at the top and at the
bottom of the grouted connection is the same as the output from the model? - would this make sense to confirm the accuracy of my model?
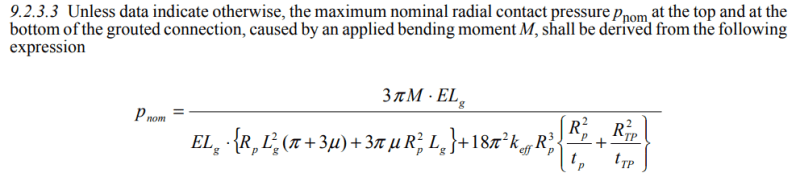
Can I use this for comparison - find spring "action force" model and see if its the same as the equation?
