I'm designing a pumping system where I have a large variance in flow and the starting Elevaiton is higher than my end elevation. So at low flow, I would not stay on the pump curve. However, at the peak flow, I am on the curve due to line losses. I'm considering installing a backpressure valve on the line to maintain a minimum pressure in the line so the pump is always on the curve. Does this backpressure valve act as a static pressure loss that is always present in the line? As an example:
Lets say my pump needs to have at least 10 psi of backpressure to stay on the curve at a good spot. So I set my backpressure regulator at 10 psi. During peak flow, my line loss (assume 12 psi) downstream of the backpressure will exceed my backpressure regulator setpoint. Ignoring elevation head, would my pump see a velocity head loss of 22 psi?
Thanks in advance.
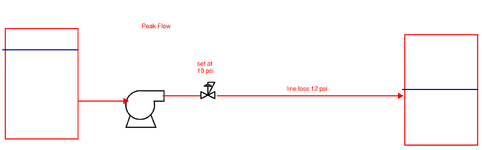
Lets say my pump needs to have at least 10 psi of backpressure to stay on the curve at a good spot. So I set my backpressure regulator at 10 psi. During peak flow, my line loss (assume 12 psi) downstream of the backpressure will exceed my backpressure regulator setpoint. Ignoring elevation head, would my pump see a velocity head loss of 22 psi?
Thanks in advance.
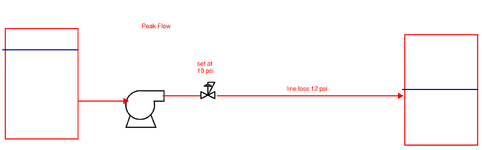