Hello all,
I'm hoping someone here can help me understand if I have modeled something correctly (Moment releases). Or if someone that has good experience can help me understand if the software is working in the way I would believe by intuition. I have little experience with these type software.
Below are screenshots of my situation. The issue is at the bottom center 45 degree bend.
In reality, I plan to use a double 2x12 as the rim joist and I plan to have member 76 tie into member 61 with a double skewed joist hanger. I have released all moments x,y,z at the end of member 61. The loading will be transferring from the left end of 76 into the joist hanger than is attached to the face of the end of 61
Is this the correct way to model this?
Also, i have one other concern and it is about "feel"/ bounciness etc.
This design is a little abnormal in that I have created an unsupported joint at the interface of 61 and 76. The distance from the left support post- 51- a 6x6 is 2.5', The distance form the right 6x6, 52, is 6'. 2x10 Joist are on 1' centers. The joist span is 14'. Post height 8'. (I hear, it is best practice to have a post at this joint. I would rather not because the post ends up being in the middle of a doorway sightline.-- this can be seen in the last screenshot section view)
How do I determine if I will have any bounciness? Can anyone here give any experience with these situations as I have none.
I have not done a code check on this design yet so I don't have the results of stress but I don't expect failures (maybe I'll be wrong). The displacement results are .325" max displacement at CL of joist. Rims show less than 1/16" displacement. (Some Rims show deflection in the positive direction. I assume that means I have uplift that I may have to account for with a post cap of proper resistance.
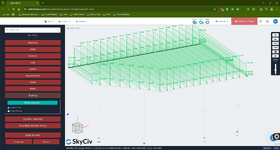

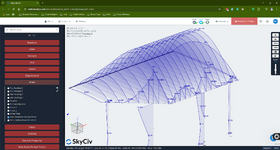
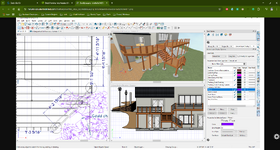
I'm hoping someone here can help me understand if I have modeled something correctly (Moment releases). Or if someone that has good experience can help me understand if the software is working in the way I would believe by intuition. I have little experience with these type software.
Below are screenshots of my situation. The issue is at the bottom center 45 degree bend.
In reality, I plan to use a double 2x12 as the rim joist and I plan to have member 76 tie into member 61 with a double skewed joist hanger. I have released all moments x,y,z at the end of member 61. The loading will be transferring from the left end of 76 into the joist hanger than is attached to the face of the end of 61
Is this the correct way to model this?
Also, i have one other concern and it is about "feel"/ bounciness etc.
This design is a little abnormal in that I have created an unsupported joint at the interface of 61 and 76. The distance from the left support post- 51- a 6x6 is 2.5', The distance form the right 6x6, 52, is 6'. 2x10 Joist are on 1' centers. The joist span is 14'. Post height 8'. (I hear, it is best practice to have a post at this joint. I would rather not because the post ends up being in the middle of a doorway sightline.-- this can be seen in the last screenshot section view)
How do I determine if I will have any bounciness? Can anyone here give any experience with these situations as I have none.
I have not done a code check on this design yet so I don't have the results of stress but I don't expect failures (maybe I'll be wrong). The displacement results are .325" max displacement at CL of joist. Rims show less than 1/16" displacement. (Some Rims show deflection in the positive direction. I assume that means I have uplift that I may have to account for with a post cap of proper resistance.
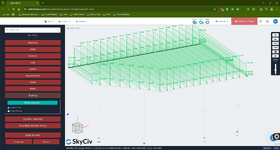

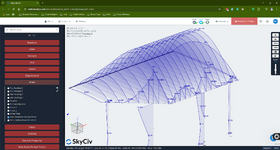
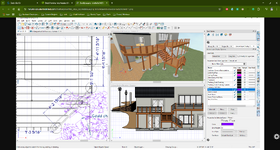