Hi,
I'm trying to figure out how to use an object's defined kinetic energy to determine if its collision with a wire will break it, assuming the wire is weaker along its length than at its mounted ends. The real scenario is a motor boat with a KE of 40,000 Kg-Meter (shouldn't the doc's specs have this in kg-m2/s2?) is ramming a marine security barrier, and I need to figure out if the components in the marine barrier system will not fail. See image below of the security barrier system for concept.
To simplify my scenario I'm assuming my 19mm weldless end links are the weakest components in the system. They are made of AISI 1035 carbon steel (link for a materials property sheet I found: I'm also assuming the boat to be a "blob" that sticks to and combines with my system at impact, so that it doesn't skip and just graze the system. The barrier is not a taught line and I'm assuming there's enough slack for there to be a 140 degree angle in the system before it becomes "taught" by the boat (see image to clarify).
My initial path was to find the strain energy required to break my end links, but I'm uncertain how to do this as I can't find the AISI 1035 carbon steel's modulus of toughness and I don't know how to apply the referenced material properties into my strain energy in terms of the normal strain energy equation Ui = ∫V(σ2/(2E))dV.
Another path I was thinking of, which seems improper to me due to the principles in the mechanics of materials, is finding the boat's impact force and seeing if this force is great enough to exceed my end link's UTS. Here, I'm uncertain of the slow down distance and not feeling comfortable to assume this figure.
Am I on the right path and can you help me? Should I be attacking this problem from a different angle?
Thank you for any help. I took my undergrad with classes in materials and mechanical engineering. It's become quite rusty.
I'm trying to figure out how to use an object's defined kinetic energy to determine if its collision with a wire will break it, assuming the wire is weaker along its length than at its mounted ends. The real scenario is a motor boat with a KE of 40,000 Kg-Meter (shouldn't the doc's specs have this in kg-m2/s2?) is ramming a marine security barrier, and I need to figure out if the components in the marine barrier system will not fail. See image below of the security barrier system for concept.
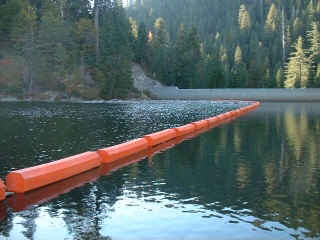
To simplify my scenario I'm assuming my 19mm weldless end links are the weakest components in the system. They are made of AISI 1035 carbon steel (link for a materials property sheet I found: I'm also assuming the boat to be a "blob" that sticks to and combines with my system at impact, so that it doesn't skip and just graze the system. The barrier is not a taught line and I'm assuming there's enough slack for there to be a 140 degree angle in the system before it becomes "taught" by the boat (see image to clarify).
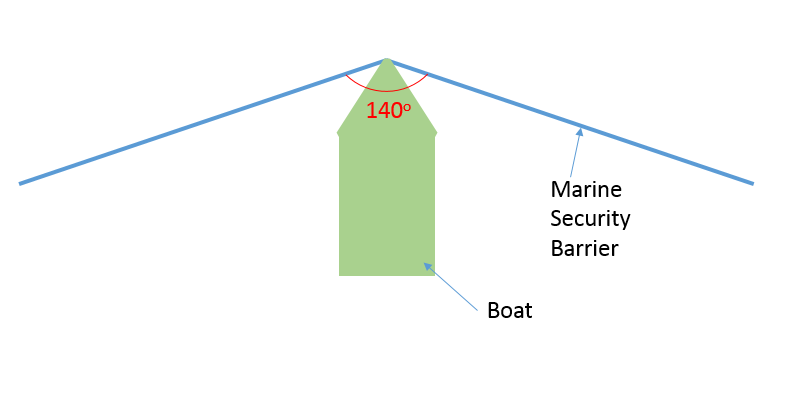
My initial path was to find the strain energy required to break my end links, but I'm uncertain how to do this as I can't find the AISI 1035 carbon steel's modulus of toughness and I don't know how to apply the referenced material properties into my strain energy in terms of the normal strain energy equation Ui = ∫V(σ2/(2E))dV.
Another path I was thinking of, which seems improper to me due to the principles in the mechanics of materials, is finding the boat's impact force and seeing if this force is great enough to exceed my end link's UTS. Here, I'm uncertain of the slow down distance and not feeling comfortable to assume this figure.
Am I on the right path and can you help me? Should I be attacking this problem from a different angle?
Thank you for any help. I took my undergrad with classes in materials and mechanical engineering. It's become quite rusty.