HydraulicsGuy
Mechanical
I have a Ridgid MEGAMax Power Base:
I have found a way to make this base power-on without having one of their 3 attachment heads attached (a project in itself!). I will be using it to drive a hydraulic pump. Pump size to be chosen based on Power Base performance. Therefore, I need to know:
(1) no-load RPM
&
(2a) stall torque or
(2b) torque at some other RPM
From those, I can calculate the RPM at any torque, or the torque at any RPM.
RPM measurement should be pretty straightforward I think. This was recommended:
My question: What is a simple cheap way to directly measure the torque? I don't want to design a test setup if I don't have to. I did some brief googling but nothing stood out, other than a reply from someone on this forum on another thread, suggesting to measure a base reaction rather than a torque at the shaft. There are no shaft RPM and torque values stated for this Power Base that I could find. There are some values, but they are for the attachment heads, and who knows what kind of gearing takes place inside those. RPM + torque values (together) are extremely difficult to come by on the internet, for any power tool. I have not tried contacting the company. Since it's not the tool's intended use, I'm 100% sure it will be met with disdain. I'm also 100% sure I'll have to correspond with a salesman, and there is only a 25% chance he'll comprehend what I'm looking for. I want to discuss with engineers.
More googling after posting this. Is the answer a "torque transducer"?
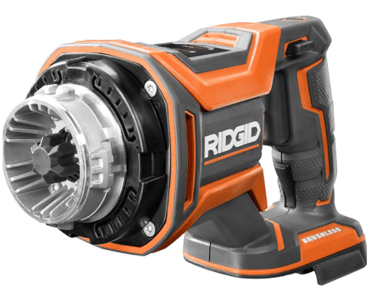
I have found a way to make this base power-on without having one of their 3 attachment heads attached (a project in itself!). I will be using it to drive a hydraulic pump. Pump size to be chosen based on Power Base performance. Therefore, I need to know:
(1) no-load RPM
&
(2a) stall torque or
(2b) torque at some other RPM
From those, I can calculate the RPM at any torque, or the torque at any RPM.
RPM measurement should be pretty straightforward I think. This was recommended:
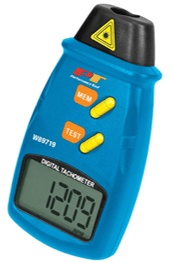
My question: What is a simple cheap way to directly measure the torque? I don't want to design a test setup if I don't have to. I did some brief googling but nothing stood out, other than a reply from someone on this forum on another thread, suggesting to measure a base reaction rather than a torque at the shaft. There are no shaft RPM and torque values stated for this Power Base that I could find. There are some values, but they are for the attachment heads, and who knows what kind of gearing takes place inside those. RPM + torque values (together) are extremely difficult to come by on the internet, for any power tool. I have not tried contacting the company. Since it's not the tool's intended use, I'm 100% sure it will be met with disdain. I'm also 100% sure I'll have to correspond with a salesman, and there is only a 25% chance he'll comprehend what I'm looking for. I want to discuss with engineers.
More googling after posting this. Is the answer a "torque transducer"?