LittleInch
Petroleum
Helicopter sight seeing inner York crashed with all dead.
This video looks like it was flying at some speed, then something happens, it seems to change orientation very rapidly which causes the whole tail structure to detach, followed shortly by the main rotor blade and part of the gearbox. Horrible way to go.
www.theguardian.com
This video looks like it was flying at some speed, then something happens, it seems to change orientation very rapidly which causes the whole tail structure to detach, followed shortly by the main rotor blade and part of the gearbox. Horrible way to go.
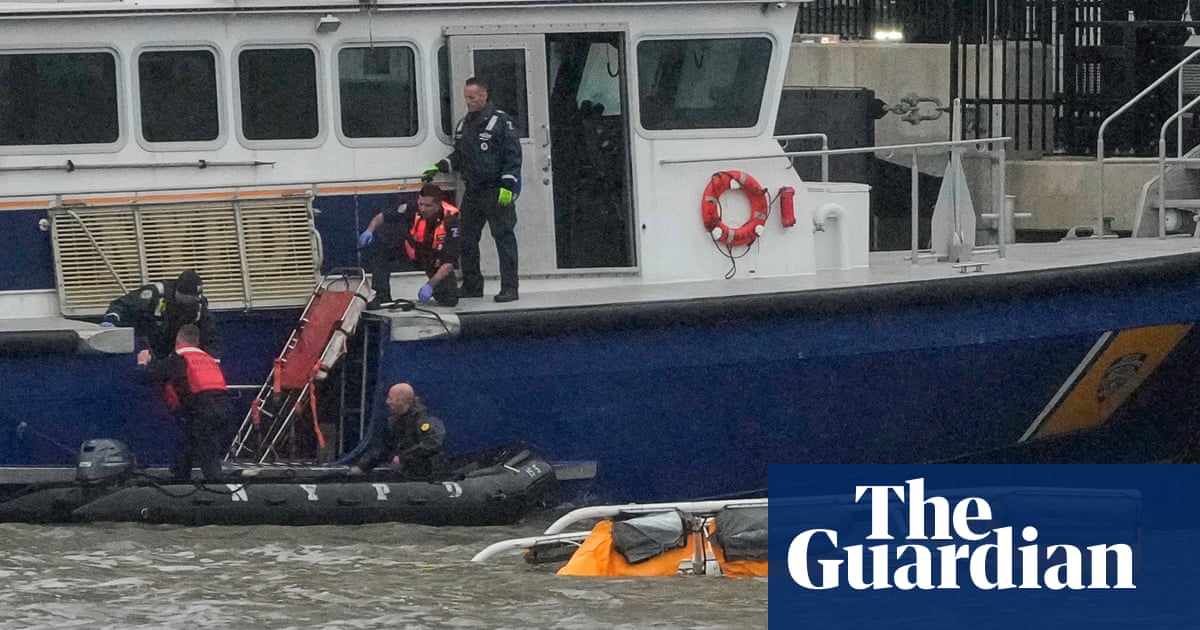
Six people killed after helicopter crashes into Hudson River in New York
Pilot and a family with three children who are believed to have been Spanish tourists were killed onboard aircraft