Hey Guys,
I have the case, where beam bearing on column cap plate which has 360kips as shear and no moment force. Shear force will be satisfied by using direct bearing. Is this necessary to design cap plate thickness and number of bolts still? If yes any way to design? Or just I need to provide cap plate thickness same as beam flange?
below from AISC (Hollow StructuralSection Connections) states cap plate thickness should be min of beam flange.
[highlight #EF2929]"The following is a simplified check provided in Part 9 of the AISC Manual based upon the “no prying action” equation.
Because tmin < tf , there is no prying action in the beam flange."[/highlight]
Beam flange thickness is 2.75"
Thanks in advance!!
I have the case, where beam bearing on column cap plate which has 360kips as shear and no moment force. Shear force will be satisfied by using direct bearing. Is this necessary to design cap plate thickness and number of bolts still? If yes any way to design? Or just I need to provide cap plate thickness same as beam flange?
below from AISC (Hollow StructuralSection Connections) states cap plate thickness should be min of beam flange.
[highlight #EF2929]"The following is a simplified check provided in Part 9 of the AISC Manual based upon the “no prying action” equation.
Because tmin < tf , there is no prying action in the beam flange."[/highlight]

Beam flange thickness is 2.75"
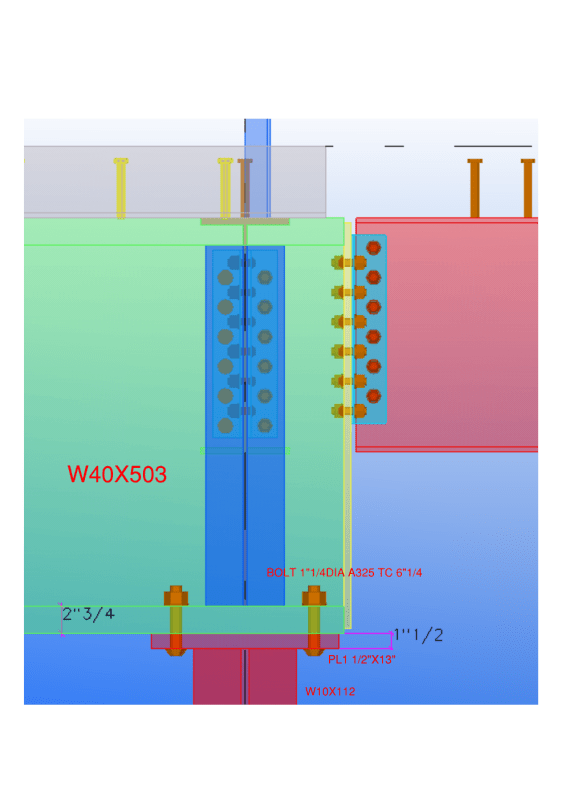
Thanks in advance!!