I have a faucet plastic component which has gaps/ interruptions along the circumference of an outside diameter. I cannot share the entire part, but something which is very similar is shown below. The outside diameter has 8 gaps around the 360° degrees which creates 8 arcs.
How can I define those 8 arcs related with a datum reference frame ?
I am using ASME 2009 (or with a note I can use 2018). I know I can use profile and position, but my question is:
Can I use CF- continuous feature per 2009 or 2018 with position ?
Can I use 8X size (.500±.015) and position?
(Profile and phantom circle is not much liked in my general industry- hence I will leave it to the last resort
)
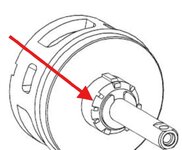
How can I define those 8 arcs related with a datum reference frame ?
I am using ASME 2009 (or with a note I can use 2018). I know I can use profile and position, but my question is:
Can I use CF- continuous feature per 2009 or 2018 with position ?
Can I use 8X size (.500±.015) and position?
(Profile and phantom circle is not much liked in my general industry- hence I will leave it to the last resort

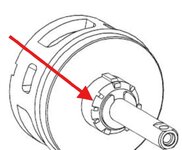