WinWin2022
Mechanical
Dear Sir/Madam!
Thank you for listening my question!
In my shop floor have conducted 1 weld joint as:
Pipe (A672-C60 CL12) + Elbow (A234-WPBW)
Filer metal: ER70S-6 2.4
We conducted PMI for this weld, result as picture
Because Cacbon steel, so when PMI is appeared Fe & Mn composition
I want to know Accept Criteria PMI for this weld (How much percent Mn be accepted?)
As result picture bellow be accepted or not?
At Pipe
At weld
At Elbow
Thank you for listening my question!
In my shop floor have conducted 1 weld joint as:
Pipe (A672-C60 CL12) + Elbow (A234-WPBW)
Filer metal: ER70S-6 2.4
We conducted PMI for this weld, result as picture
Because Cacbon steel, so when PMI is appeared Fe & Mn composition
I want to know Accept Criteria PMI for this weld (How much percent Mn be accepted?)
As result picture bellow be accepted or not?
At Pipe
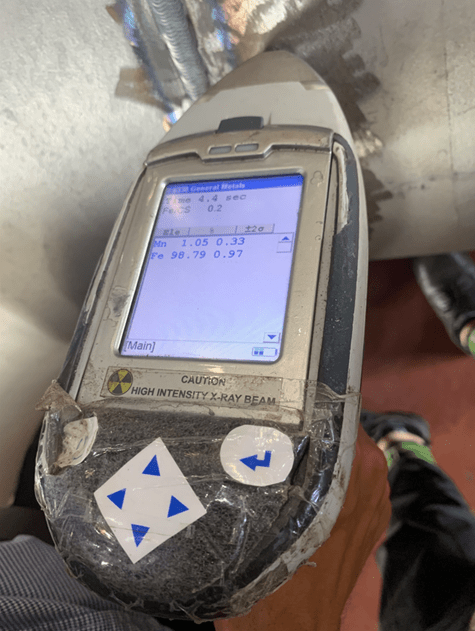
At weld
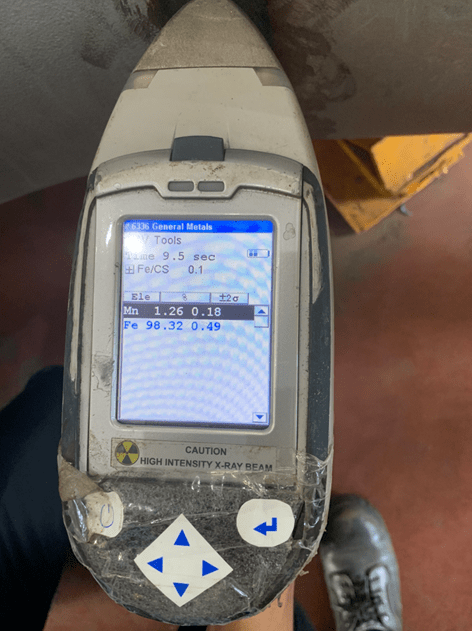
At Elbow
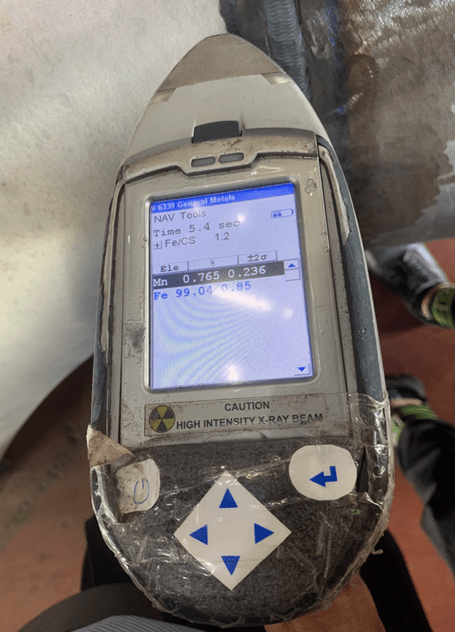