HeavenSpace
Mechanical
Hi,
I've just completed some tensile testing of 3D Printed Aluminium coupons, and the results look suspect. Can anyone shed some light as to what could have caused the initial anomaly in the Stress-Strain diagram?
A second question I have is that I am looking to tensile test coupons in the "As-printed" condition i.e. no machining, grinding, etc. I thought the test might be meaningless, since there are so many variables involved when the samples are "as is". Any comments?
I've just completed some tensile testing of 3D Printed Aluminium coupons, and the results look suspect. Can anyone shed some light as to what could have caused the initial anomaly in the Stress-Strain diagram?
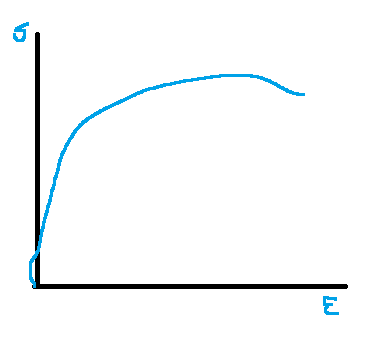
A second question I have is that I am looking to tensile test coupons in the "As-printed" condition i.e. no machining, grinding, etc. I thought the test might be meaningless, since there are so many variables involved when the samples are "as is". Any comments?
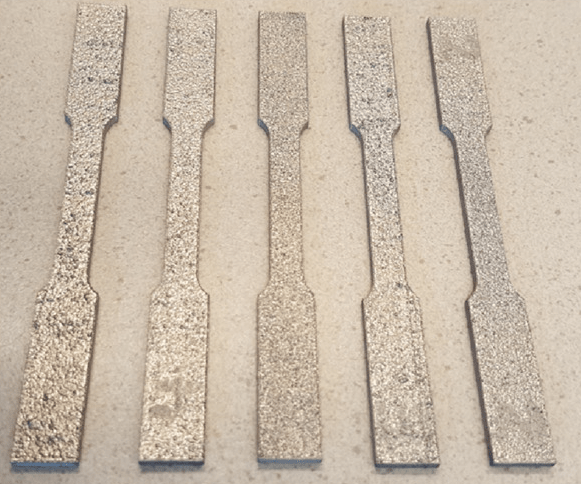