Perka
Automotive
- Feb 26, 2019
- 8
I'm new to GD&T. What's your approach of tolerancing a polygon shape.
'Profile of a surface' as in option 1 locks down a lot.
At first I thought it looked down too much so I tried Method 2 using symmetry, which in the end pretty much did the same as profile of a surface.
Then I thought of some dotted inscribed reference circle with concentricity tolerance, along with parallellism tolerance.
Brain is confused to say the least. Suggestions?
'Profile of a surface' as in option 1 locks down a lot.
At first I thought it looked down too much so I tried Method 2 using symmetry, which in the end pretty much did the same as profile of a surface.
Then I thought of some dotted inscribed reference circle with concentricity tolerance, along with parallellism tolerance.
Brain is confused to say the least. Suggestions?
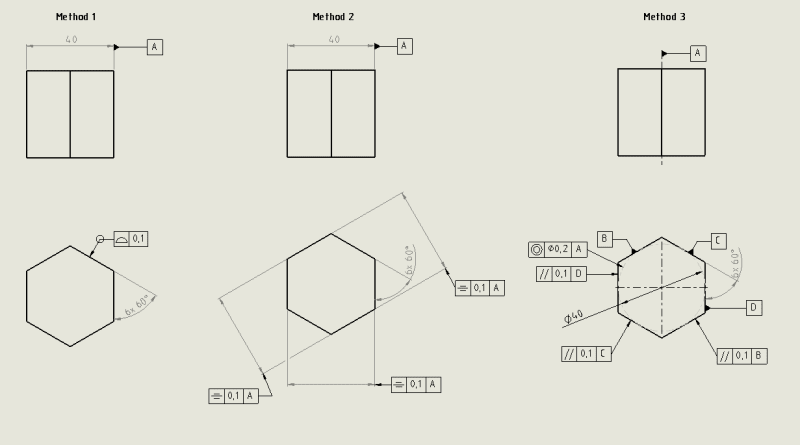