The recent thread on Surface Profile and Size brought up an interesting effect regarding tolerance zone extent.
Here is a drawing for a fictitious part, that illustrates the effect. I have intentionally avoided the use of directly toleranced dimensions.
It has been proposed that an as-produced part like the blue one would conform to the 2 mm profile tolerance to A. This doesn't seem right to me, but so far I can't point to anything in Y14.5 that would disallow this. The standard does not give much detail on the extend of tolerance zones (or datum feature simulators).
Opinions?
Evan Janeshewski
Axymetrix Quality Engineering Inc.
Here is a drawing for a fictitious part, that illustrates the effect. I have intentionally avoided the use of directly toleranced dimensions.
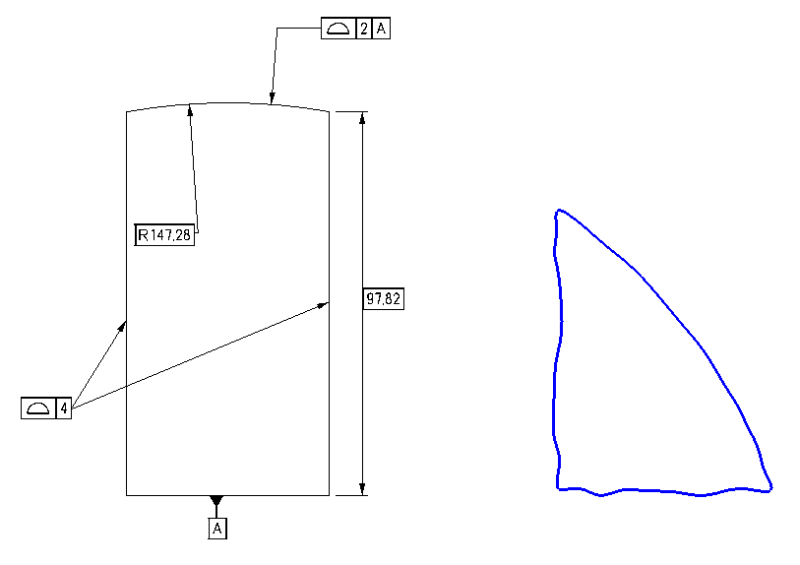
It has been proposed that an as-produced part like the blue one would conform to the 2 mm profile tolerance to A. This doesn't seem right to me, but so far I can't point to anything in Y14.5 that would disallow this. The standard does not give much detail on the extend of tolerance zones (or datum feature simulators).
Opinions?
Evan Janeshewski
Axymetrix Quality Engineering Inc.