psychedomination
Structural
Hi there,
I am trying to determine if this connection is adequate for the loads that are applied. There is a 50kN force acting on the steel plate in opposite directions in the y axis.
The main fear was that the hook holes were too close to the edge and that they would tear through the end of the steel plate. Either a hook or shackle will be connected to the hole.
I originally did the following calculation but am unsure if it is adequate.
Effective shear area in the plane (thickness of plate * distance from edge of hole to end of plate) * Shear stress of steel ... taking the shear stress of steel as 0.6* yield stress
(50-38/2)* 16* 150 = 74.4 kN. ... Therefore would be OK.
However, I am not confident. Any advice on the calculations would be greatly appreciated.
I am trying to determine if this connection is adequate for the loads that are applied. There is a 50kN force acting on the steel plate in opposite directions in the y axis.
The main fear was that the hook holes were too close to the edge and that they would tear through the end of the steel plate. Either a hook or shackle will be connected to the hole.
I originally did the following calculation but am unsure if it is adequate.
Effective shear area in the plane (thickness of plate * distance from edge of hole to end of plate) * Shear stress of steel ... taking the shear stress of steel as 0.6* yield stress
(50-38/2)* 16* 150 = 74.4 kN. ... Therefore would be OK.
However, I am not confident. Any advice on the calculations would be greatly appreciated.
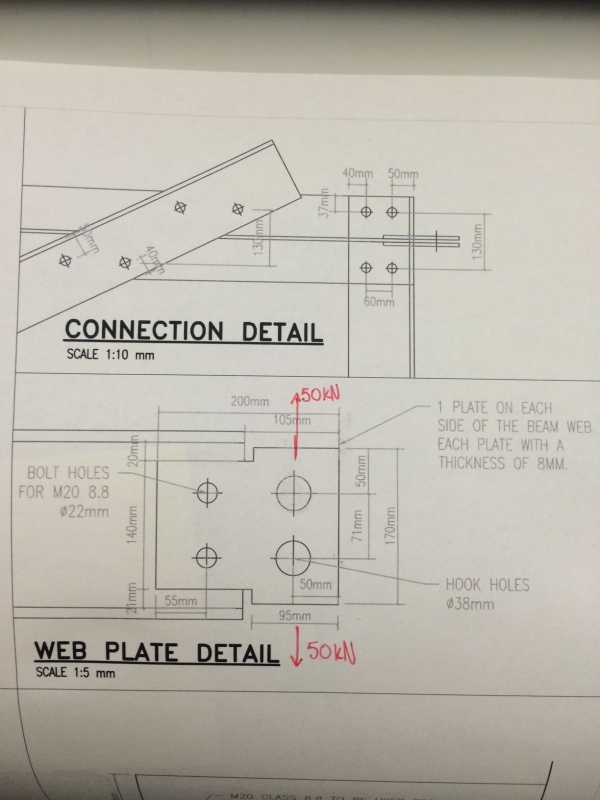