Dear all,
I have a Div. 1 vessel with top 36" nozzle, 600# B16.47 series A, connected to a forging flange with hub ( we call it reducing flange) and a 18" outlet pipe as shown.
Can this reducing flange be classified as custom made component, not fitting UG-34, UG-39, Appendix 2 or Div 2 Part 4, such that it meets Div. 1 46-4, "Design by Analysis", and using FEA only per Div. 2 Part 5 is acceptable ?
(Note, using UG-34, UG-39 or Appendix 2 will end up much thicker than standard 36" flange)
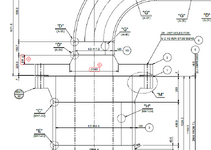
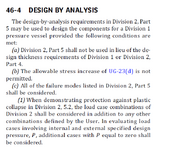
I have a Div. 1 vessel with top 36" nozzle, 600# B16.47 series A, connected to a forging flange with hub ( we call it reducing flange) and a 18" outlet pipe as shown.
Can this reducing flange be classified as custom made component, not fitting UG-34, UG-39, Appendix 2 or Div 2 Part 4, such that it meets Div. 1 46-4, "Design by Analysis", and using FEA only per Div. 2 Part 5 is acceptable ?
(Note, using UG-34, UG-39 or Appendix 2 will end up much thicker than standard 36" flange)
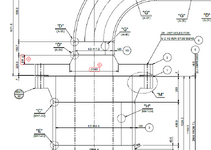
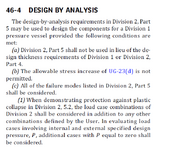