I was recently tasked with designing a small leachate pumpstation servicing an odour control biofilter. The static head is quite low at about 3m that discharges to a terminal pumpstation that receives pumped flow from multiple other wastewater pumpstations.
I got thinking that if i connected a rising main from the leachate wetwell into one of the other rising mains with a y-junction and a low head non-return valve (like a wastop valve) would the flow from the pumped pipe across the junction create enough negative pressure on the leachate pipe that it doesn't require a pump in the leachate wetwell? (in this configuration the static head could be reduced to 2m, possibly less, leachate pipe would be about 20m.
In theory i think this could work and just curious about it as i have already finished the design. but not sure how i would even calculate this. It may only work if the velocity in the pumped main was massive.
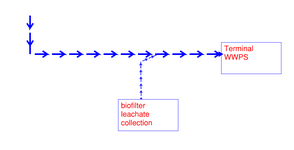
I got thinking that if i connected a rising main from the leachate wetwell into one of the other rising mains with a y-junction and a low head non-return valve (like a wastop valve) would the flow from the pumped pipe across the junction create enough negative pressure on the leachate pipe that it doesn't require a pump in the leachate wetwell? (in this configuration the static head could be reduced to 2m, possibly less, leachate pipe would be about 20m.
In theory i think this could work and just curious about it as i have already finished the design. but not sure how i would even calculate this. It may only work if the velocity in the pumped main was massive.
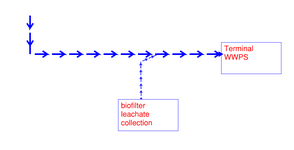