Brad805
Structural
- Oct 26, 2010
- 1,518
I am designing a connection for a precast concrete project. This is a delegated design project, and the feedback from the EOR is not stellar. In many cases we are doing projects that are designed as tilt-up, but for any number of reasons the GC decides to precast the project. Due to that, most of these EOR's are far more familiar with tilt design req'ts. Clause 21.7 of the CSA tilt up section (below) has a special design requirement for the connections. There is not a similar clause in 21.8 for precast concrete. I have had discussions with others and some feel this clause applies and others believe it does not. I tend to err on the side of caution. The Rd=1.5, Ro=1.3 for this building. This clause requires that non-ductile connection should be designed for a force determined using an RdRo=1.3 instead of RdRo=1.95. The building is located in a very low seismic region.
Question:
1. Below you can see an image of the connection. This is a dry connection consisting of an embed plate, and A706 rebars. Design of the weld for RdRo=1.3 is easily accomplished. Would you design the embedded elements for RdRo=1.3 or 1.95? Obviously, the conservative approach would be to use the increased load, but when I do the connection is causing a great deal of difficulty.
For Koot's anchorage theory I have included a screenshot of the analysis model. This is an image of the connection with a shear load =200kN and axial =200kN. You can see the cracking starting in the shape as a breakout. I stopped the analysis at this point since it was no longer converging properly. I thought I would include this out of interest.
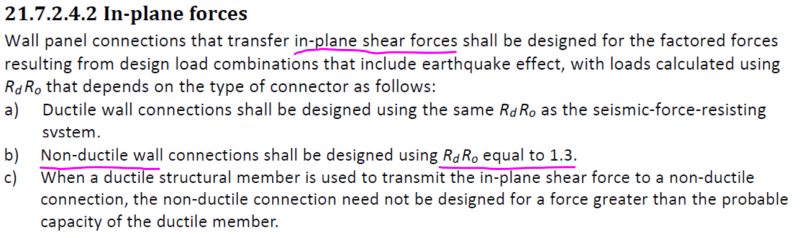
Question:
1. Below you can see an image of the connection. This is a dry connection consisting of an embed plate, and A706 rebars. Design of the weld for RdRo=1.3 is easily accomplished. Would you design the embedded elements for RdRo=1.3 or 1.95? Obviously, the conservative approach would be to use the increased load, but when I do the connection is causing a great deal of difficulty.
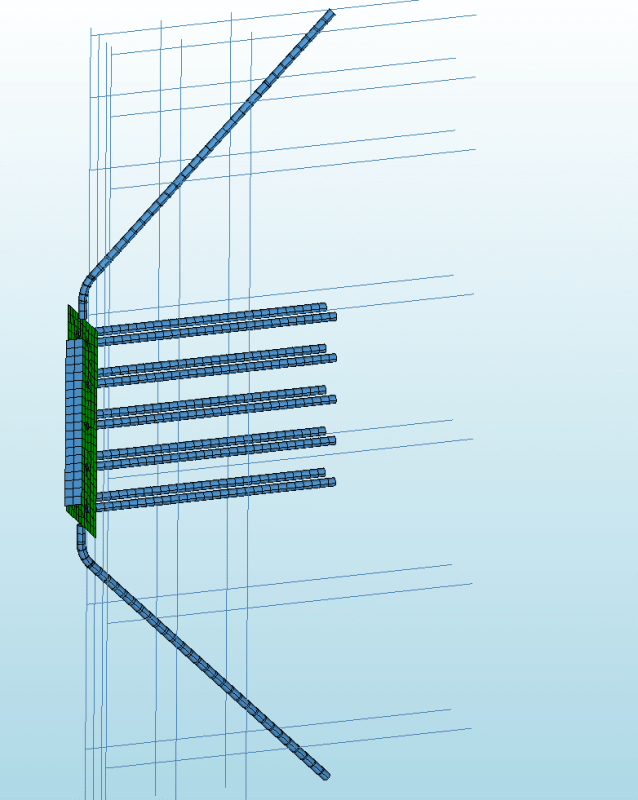
For Koot's anchorage theory I have included a screenshot of the analysis model. This is an image of the connection with a shear load =200kN and axial =200kN. You can see the cracking starting in the shape as a breakout. I stopped the analysis at this point since it was no longer converging properly. I thought I would include this out of interest.
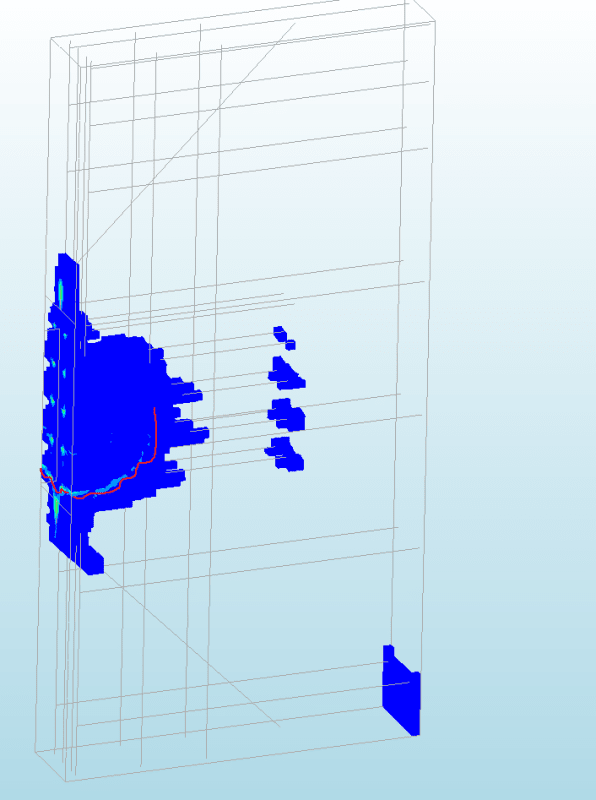