Hi,
I'm building a mobile robot to demonstrate an agricultural spraying robot. The robot has two motors that drive the skid steer (6v @ 2A each) and a water pump (12v @ 4A) taken from a car windshield washer pump. I have an Arduino equipped with Wifi, GPS and a few other sensors (IMU, LEDs) which is providing PWM signals to a cheap-o 4-axis DC motor driver.
I'm using a smartphone power bank (1 x 5v, 5000mah) for the Arduino and its electronics and 4 x AA NiMh batteries in a pack for the motor drivers
Its a pain dealing with many batteries, have no ability to detect charge levels, and in general very messy with lots of cables. I've also noticed that the powerbank for the Arduino is unable to supply 1.5A consistently with WiFi running and GPS running.
I recently found and broke open a 10,000mah Li-ion power bank and found five 2Ah batteries connected in parallel.
I'm now thinking of rebuilding a single rechargeable battery pack from these batteries!
Is there anyway I can achieve what's in the diagram using off-the-shelf electronics from Digi-Key or other supplier?
What I want as features are:
- Uninterrupted power for motors and Arduino from battery and recharge at the same time from wall supply (like a smartphone)
- Same battery should provide stable 2A @ 5V to the Arduino and electronics without drops while the motors are running
- Same battery should power the three motors irrespective if one, two or three are running at anytime.
- Battery should provide feedback on its charge level
Is this even possible? I'm no expert in battery electronics and scared that I might create a fire if I'm not careful. Given that the battery cells will drop their voltages very low due to the high loads, I'm even wondering if the Li Ion batteries will survive or be able to recharge at all.
I know a lot of mobile robots like Roomba, Double and others have internal rechargeable batteries but I'm not sure how they manage the same issues and power the motors at the same time, particularly with Li-Ion batteries.
Any help is much appreciated!
I'm building a mobile robot to demonstrate an agricultural spraying robot. The robot has two motors that drive the skid steer (6v @ 2A each) and a water pump (12v @ 4A) taken from a car windshield washer pump. I have an Arduino equipped with Wifi, GPS and a few other sensors (IMU, LEDs) which is providing PWM signals to a cheap-o 4-axis DC motor driver.
I'm using a smartphone power bank (1 x 5v, 5000mah) for the Arduino and its electronics and 4 x AA NiMh batteries in a pack for the motor drivers
Its a pain dealing with many batteries, have no ability to detect charge levels, and in general very messy with lots of cables. I've also noticed that the powerbank for the Arduino is unable to supply 1.5A consistently with WiFi running and GPS running.
I recently found and broke open a 10,000mah Li-ion power bank and found five 2Ah batteries connected in parallel.
I'm now thinking of rebuilding a single rechargeable battery pack from these batteries!
Is there anyway I can achieve what's in the diagram using off-the-shelf electronics from Digi-Key or other supplier?
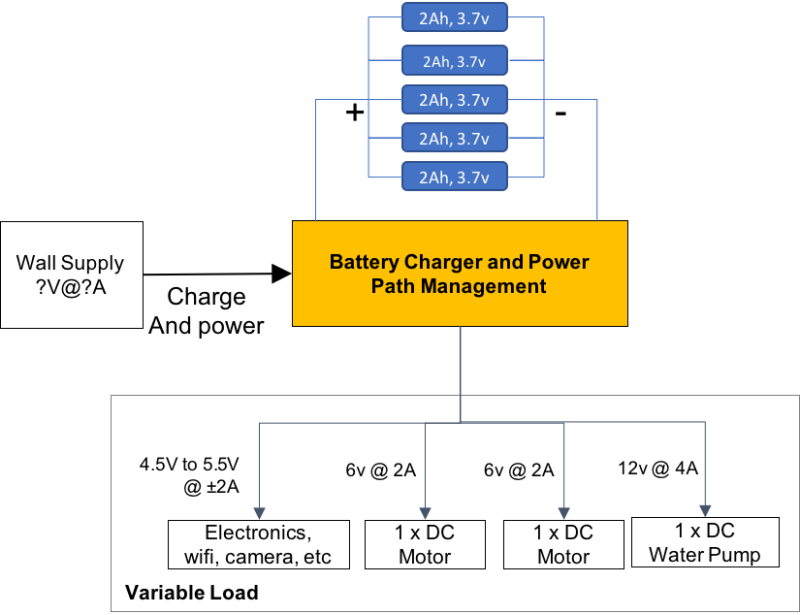
What I want as features are:
- Uninterrupted power for motors and Arduino from battery and recharge at the same time from wall supply (like a smartphone)
- Same battery should provide stable 2A @ 5V to the Arduino and electronics without drops while the motors are running
- Same battery should power the three motors irrespective if one, two or three are running at anytime.
- Battery should provide feedback on its charge level
Is this even possible? I'm no expert in battery electronics and scared that I might create a fire if I'm not careful. Given that the battery cells will drop their voltages very low due to the high loads, I'm even wondering if the Li Ion batteries will survive or be able to recharge at all.
I know a lot of mobile robots like Roomba, Double and others have internal rechargeable batteries but I'm not sure how they manage the same issues and power the motors at the same time, particularly with Li-Ion batteries.
Any help is much appreciated!