Hello,
I am trying to understand why the planetary gearbox manufacturer recommends mounting his planetary gearbox through the High Torque (Low Speed) side.
I tried to figure out what is the reason, but unfortunately he didn't reply.
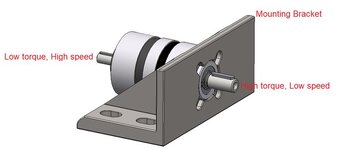
A colleague told me I would better mount the gearbox through the High Torque (Low Speed) side, because otherwise "I will transfer all of the generated forces through the gearbox housing", and I am not sure I understood what he meant.
I tried to use a simplified FBD (Force Body Diagram) to analyze the reactions on the gearbox housing in both optional mounting cases (through the High or Low torque side), and it seems that in both cases the gearbox housing reaction would be the same – tangential friction forces (under the bolts' heads) that resist the same torque, no matter to which side it's connected.
Am I missing something?
Thanks!
I am trying to understand why the planetary gearbox manufacturer recommends mounting his planetary gearbox through the High Torque (Low Speed) side.
I tried to figure out what is the reason, but unfortunately he didn't reply.
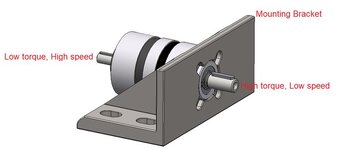
A colleague told me I would better mount the gearbox through the High Torque (Low Speed) side, because otherwise "I will transfer all of the generated forces through the gearbox housing", and I am not sure I understood what he meant.
I tried to use a simplified FBD (Force Body Diagram) to analyze the reactions on the gearbox housing in both optional mounting cases (through the High or Low torque side), and it seems that in both cases the gearbox housing reaction would be the same – tangential friction forces (under the bolts' heads) that resist the same torque, no matter to which side it's connected.
Am I missing something?
Thanks!