There is a hairline to 1/8” crack in this 5’ x 2’ x 18’ concrete pillar. The pillar is not load-]bearing, however, it is integrated into the foundation wall of the house. The homeowner noticed bubbling in the stucco, and had it removed for further investigation as is shown in the picture. The top of the pillar is stuccoed and there are some hairline cracks in it. To the right of the pillar is an upper basin and waterfall feature. No cracks were observed in the foundation wall from within the basement.
The house is 20 years old and the crack was only recently noticed.
I’m thinking that water may have gotten into the column from the top (rain) or from the side (water basin) thru a shrinkage crack and frozen. Could it also potentially be pent-up casting stresses that just decided to “let loose”? Seems like a big pour and the lateral rebar would be pretty important. I designed the wood framing for the house and my colleague did the concrete, but he has since passed, and I don’t have his records that far back.
Any thoughts?
Thanks!
The house is 20 years old and the crack was only recently noticed.
I’m thinking that water may have gotten into the column from the top (rain) or from the side (water basin) thru a shrinkage crack and frozen. Could it also potentially be pent-up casting stresses that just decided to “let loose”? Seems like a big pour and the lateral rebar would be pretty important. I designed the wood framing for the house and my colleague did the concrete, but he has since passed, and I don’t have his records that far back.
Any thoughts?
Thanks!
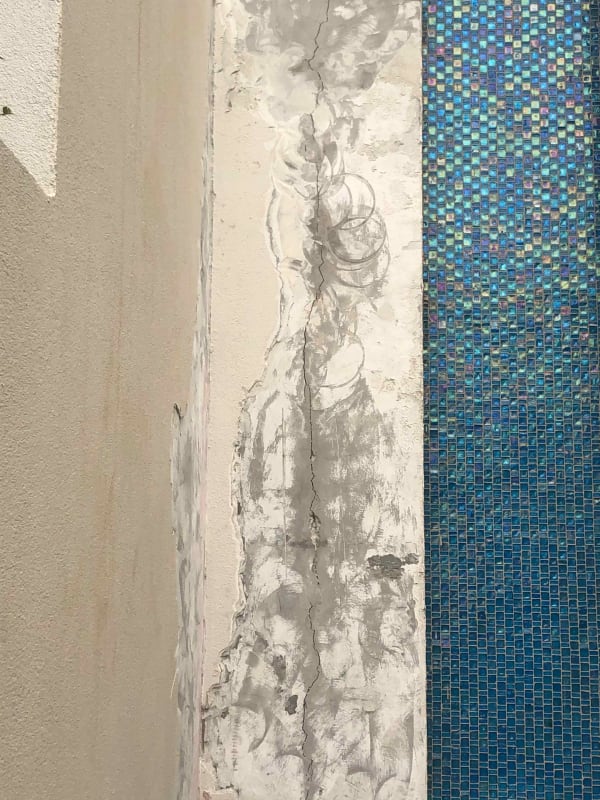
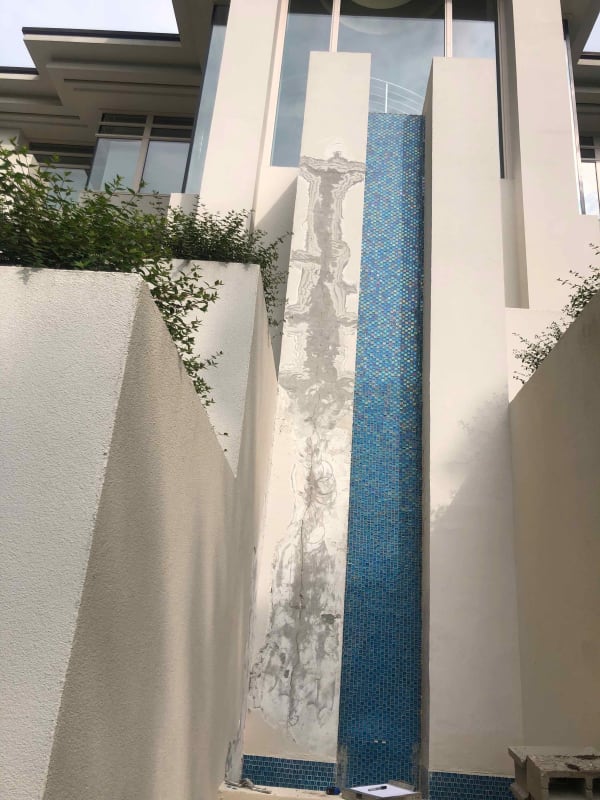