mats12
Geotechnical
- Dec 17, 2016
- 181
Its a small structure but I want to model it correctly. Im looking for some good advice.
I have to design a small steel canopy roof on top of a steel barn with light polycarbonate roof plates on top of it.
This canopy is made of transverse steel frames (all elements welded together) and longit. steel beams that are bolted between steel frames.
All sections are hollow: 80 x 40 x 4 mm
Would you consider connections between elements of welded transverse frames as moment connections or as pinned?
(If i use pinned connections I get much larger moments and deflections in my frame)
Critical is the connection between a steel column and beam (connection A). I think I should use some additional reinf. steel plates there to make it more stiff/rigid. What do you suggest?
Im also wondering what would you do about horizontal stability of this conopy. Making X bracing in a roof plane or something similar seems overkill.
I have to design a small steel canopy roof on top of a steel barn with light polycarbonate roof plates on top of it.
This canopy is made of transverse steel frames (all elements welded together) and longit. steel beams that are bolted between steel frames.
All sections are hollow: 80 x 40 x 4 mm
Would you consider connections between elements of welded transverse frames as moment connections or as pinned?
(If i use pinned connections I get much larger moments and deflections in my frame)
Critical is the connection between a steel column and beam (connection A). I think I should use some additional reinf. steel plates there to make it more stiff/rigid. What do you suggest?
Im also wondering what would you do about horizontal stability of this conopy. Making X bracing in a roof plane or something similar seems overkill.
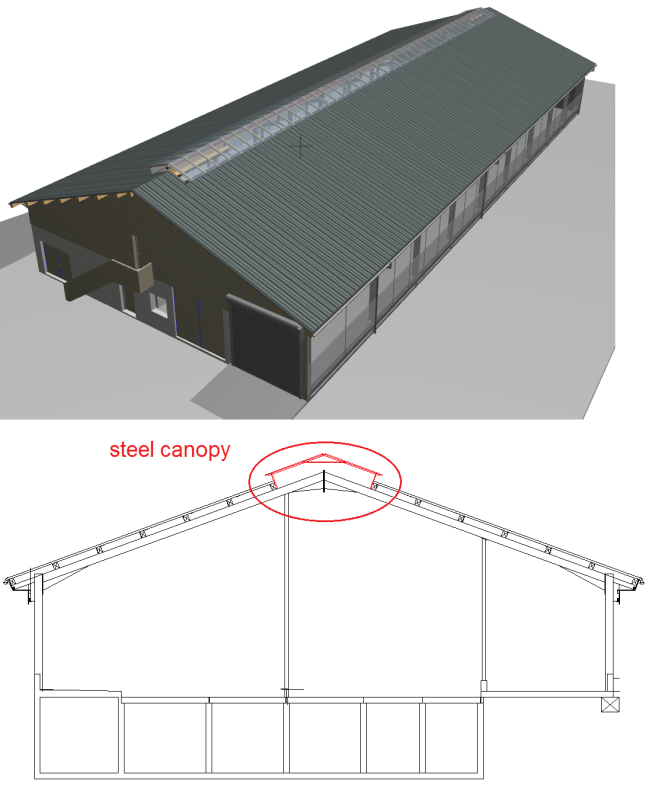
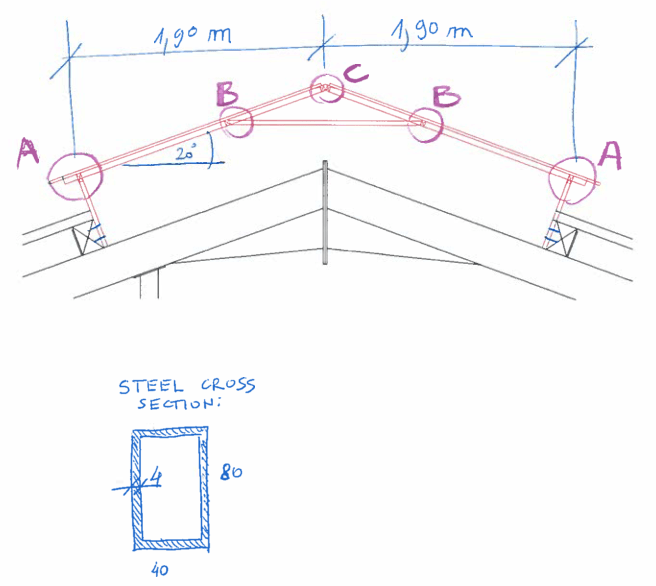
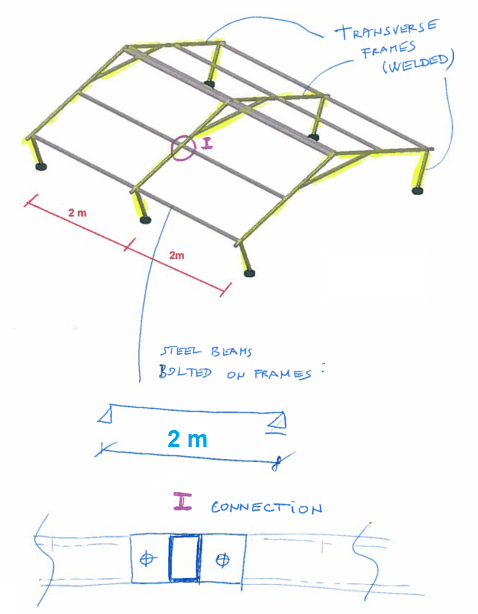