Ron247
Structural
- Jan 18, 2019
- 1,182
I have an architect who wants a front drive thru that extends about 21' from the building. He has "envisioned" 3 roof trusses (2 ends and a center) to support the drive thru roof that he wants to be made out of circles and not triangular pieces. I have made several suggestions how to get a similar appearance but he wants to be able to see through the circles as part of the look. In the drawing below, the circles are hollow even though the shading indicates they are solid. There is no snow to design for. The roof DL+LL is about 21 psf, so there is no excessive loading.
Any thoughts on a method to achieve this appearance but make a structure that fits his "vision"? Also, is there a way to may a truss with circles? If there is, I missed that day in Truss 101. The circles are about 18" in diameter in the picture. There is only about 2" of solid metal between circles. From a steel beam depth perspective, the beam would be about 21" tall or more. As usual, the cost is no issue now, but I know it will become and issue when someone finds out how much this is going to cost. Rolling a beam will take 3 pieces rolled that then have to be welded together to form the roller coaster part of the roof. The cost for rolling only is $5k to make all 3 frames. Does not include the cost of the beam and the welding later.
Any thoughts on a method to achieve this appearance but make a structure that fits his "vision"? Also, is there a way to may a truss with circles? If there is, I missed that day in Truss 101. The circles are about 18" in diameter in the picture. There is only about 2" of solid metal between circles. From a steel beam depth perspective, the beam would be about 21" tall or more. As usual, the cost is no issue now, but I know it will become and issue when someone finds out how much this is going to cost. Rolling a beam will take 3 pieces rolled that then have to be welded together to form the roller coaster part of the roof. The cost for rolling only is $5k to make all 3 frames. Does not include the cost of the beam and the welding later.
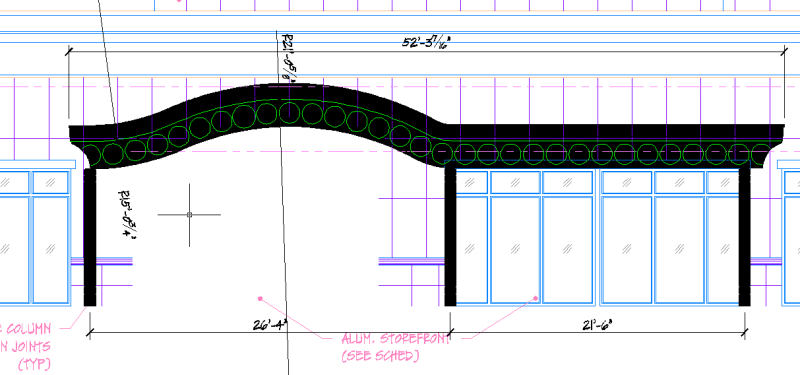