SinaPeugeot
Structural
Hi all,
We’re working on a large model with a complex contact condition; however, we’re getting some unreasonable results. We’ve pinned down the problem to a strange issue with the explicit solver. I’ve made a small model (*.inp files attached; figure shown below) which clearly shows the issue. The model consists of a series of blocks which all have contact (coef. Friction = 1.0) with each other. They are first vertically compressed (from above by ~900kN), and then the upper blocks are pushed sideways to slide over the lower blocks. Each small block is meshed with more than a dozen C3D8R element (mesh is not shown in the figure).
The expected outcome is that the blocks don’t move until the force is ~900kN (i.e., the frictional resistance = mu*N) and then sliding will initiate and the force would be constant at 900kN. This is exactly what happens when the implicit/quasi-static solver is used. However, when the exact same model is re-run using the explicit solver, the frictional resistance reduces by ~50%! Please see the figure below for a comparison of the results. I haven’t been able to identify the reason (I have looked at a slower application of the load; introducing contact damping; etc. but with no luck)
In our larger model, the difference between the theoretical friction force and that found from the explicit solver is even more drastic; but we must use the explicit solver for this analysis.
Would really appreciate any advice.
Thank you.
We’re working on a large model with a complex contact condition; however, we’re getting some unreasonable results. We’ve pinned down the problem to a strange issue with the explicit solver. I’ve made a small model (*.inp files attached; figure shown below) which clearly shows the issue. The model consists of a series of blocks which all have contact (coef. Friction = 1.0) with each other. They are first vertically compressed (from above by ~900kN), and then the upper blocks are pushed sideways to slide over the lower blocks. Each small block is meshed with more than a dozen C3D8R element (mesh is not shown in the figure).
The expected outcome is that the blocks don’t move until the force is ~900kN (i.e., the frictional resistance = mu*N) and then sliding will initiate and the force would be constant at 900kN. This is exactly what happens when the implicit/quasi-static solver is used. However, when the exact same model is re-run using the explicit solver, the frictional resistance reduces by ~50%! Please see the figure below for a comparison of the results. I haven’t been able to identify the reason (I have looked at a slower application of the load; introducing contact damping; etc. but with no luck)
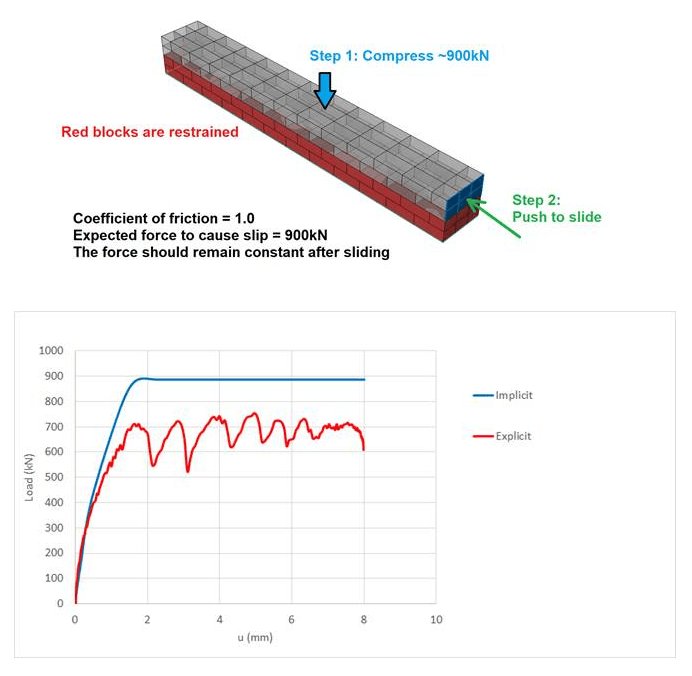
In our larger model, the difference between the theoretical friction force and that found from the explicit solver is even more drastic; but we must use the explicit solver for this analysis.
Would really appreciate any advice.
Thank you.