I have a situation where a house transitions from a crawl space to a basement. The crawl space area immediately adjacent to the basement wall was not backfilled and the first row of interior piers for the crawl space are very close to the 8'+ drop-off. There has been soil sloughing off over time near the piers.
I told the Owner of the possible remedies, and they decided they want to fill the area with flowable fill. I have suggested doing it in 3-4 lifts and letting each lift set up before installing the next lift.
I have questions:
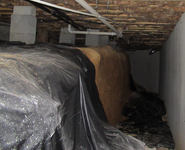
I told the Owner of the possible remedies, and they decided they want to fill the area with flowable fill. I have suggested doing it in 3-4 lifts and letting each lift set up before installing the next lift.
I have questions:
- Am I correct that once the concrete cures, the lateral form pressure from that pour is no longer present against the concrete basement wall other than any lateral soil pressure from the embankment that may have "shifted" during the pour?
- I recommended placing plastic across the bottom and up each side at least equal to the total pour height to help prevent liquid/flowable fill from seeping into the finished basement area due to the pressure. Is that reasonable to expect? It looks like the concrete wall sets on stone, not a concrete foundation.
- I did not design the concrete wall but it was a manufactured product that was installed by the supplier. I am having owner's get confirmation from supplier it is designed for lateral soil loads of the expected height. Is there more I should have them confirm?
- The finished floor above is wood. I have recommended well ventilating the crawl space during curing to minimize effects from the heat and moisture from the drying process of the flowable fill. Is that a reasonable expectation.
- Anyone ever do this before, and if so, what problems did you encounter?
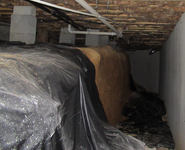