I have modeled a beam as fixed-fixed. The reaction forces are -1494 lb.ft and 761 lb (vertical). There is no horizontal reaction.
Now I know this beam is welded to another element. I am trying to design the weld for the necessary forces. How do I transfer the reaction forces at the fixed end to the weld? Should I invert the directions of the reactions or should I preserve the same directions?
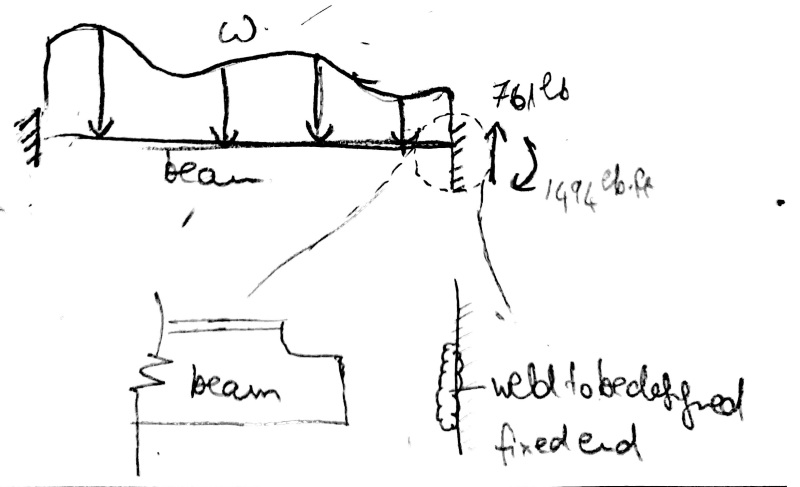
Now I know this beam is welded to another element. I am trying to design the weld for the necessary forces. How do I transfer the reaction forces at the fixed end to the weld? Should I invert the directions of the reactions or should I preserve the same directions?