Hello, I have scenario where a flat plate is welded inside a ridged cylinder with top and bottom fillet welds all the way around and pressure on top. Im trying to figure out how to calculate the bending stress in the fillet welds. I was thinking I could approximate it like the following beam example where "b" is the circumference of the ID of the ridged cylinder. However, even with this approximation I'm struggling to figure out what to use for "M". For clamped flat plate stress calculations the radial bending is calculated in terms of lbf-in/in then divided by plate thickness squared to get in terms of stress. Not sure what bending moment could be approximated as in terms of lbf-in to be able to fit in the beam weld stress equation below.

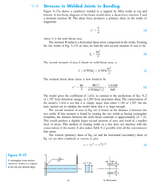

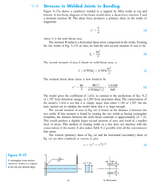