Hello Fellow engineers, I need your help with this one
My client wants to install new equipment to the roof of a building (Equipement will be attached to existing steel beams)
For this to happen, the existing beams needs to be reinforced beforehand.
My only two options are : bolting or welding a new a plate to the existing beam to increase its capacity.
After some research (googling), here is what I learned about the difference between the two options.
Welding : [ul]
[li]The building is very old and I am not even sure if the steel is weldable (investigation/destructive testing required?)[/li]
[li] Welding requires prepping, cleaning and removing paint from the existing beams (maybe expensive)[/li]
[li] The beam is already stressed (under dead and live load), welding may decrease the capacity of the beam temporarily (because of the heat) and shoring is rerquired[/li]
[li] The beam is on the roof, I do not know if it's feasable to weld.[/li]
[/ul]
Bolting : [ul]
[li]May increase local stress and might also require shoring (I am not sure how to quantify the stress).[/li]
[li]Possibly decreases existing beam capacity?[/li]
[li]To me it seems easier than welding and also less expensive ( I am not sure, I have 0 experience in the field)[/li]
[/ul]
My problem is that I still don't know which option is the best? what do you think?
Thank you in advance.
![[smile] [smile] [smile]](/data/assets/smilies/smile.gif)
My client wants to install new equipment to the roof of a building (Equipement will be attached to existing steel beams)
For this to happen, the existing beams needs to be reinforced beforehand.
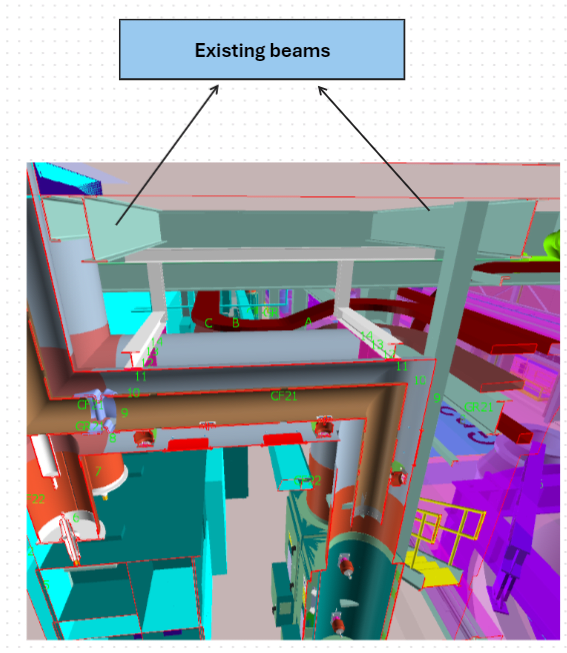
My only two options are : bolting or welding a new a plate to the existing beam to increase its capacity.
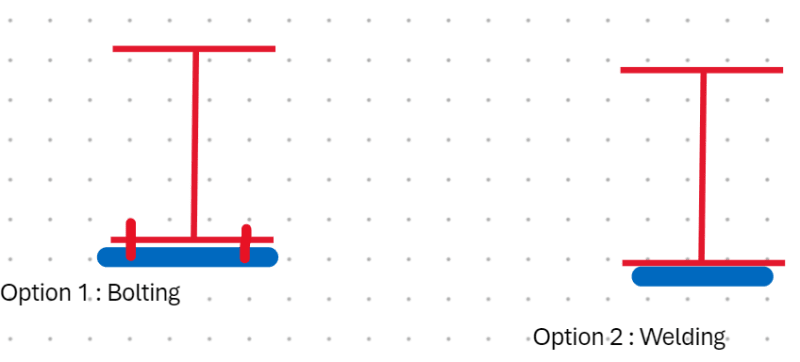
After some research (googling), here is what I learned about the difference between the two options.
Welding : [ul]
[li]The building is very old and I am not even sure if the steel is weldable (investigation/destructive testing required?)[/li]
[li] Welding requires prepping, cleaning and removing paint from the existing beams (maybe expensive)[/li]
[li] The beam is already stressed (under dead and live load), welding may decrease the capacity of the beam temporarily (because of the heat) and shoring is rerquired[/li]
[li] The beam is on the roof, I do not know if it's feasable to weld.[/li]
[/ul]
Bolting : [ul]
[li]May increase local stress and might also require shoring (I am not sure how to quantify the stress).[/li]
[li]Possibly decreases existing beam capacity?[/li]
[li]To me it seems easier than welding and also less expensive ( I am not sure, I have 0 experience in the field)[/li]
[/ul]
My problem is that I still don't know which option is the best? what do you think?
Thank you in advance.