nivoo_boss
Structural
Hey everyone!
I have to design a support platform for some machinery. The manufacturer has given me dynamic loads that I should apply to the supporting structure. The machine is quite small and light and the forces are small as well. Below is a screenshot of the table with these dynamic forces.
The problem is I have never applied dynamic forces in my software (SCIA) and I'm not well versed with dynamic design. Since the loads are very small (maximum vertically around 800 N, that's 80 kgf), would it be acceptable if I just multiply these values with a factor of 5 or something and use static design
?
I have to design a support platform for some machinery. The manufacturer has given me dynamic loads that I should apply to the supporting structure. The machine is quite small and light and the forces are small as well. Below is a screenshot of the table with these dynamic forces.
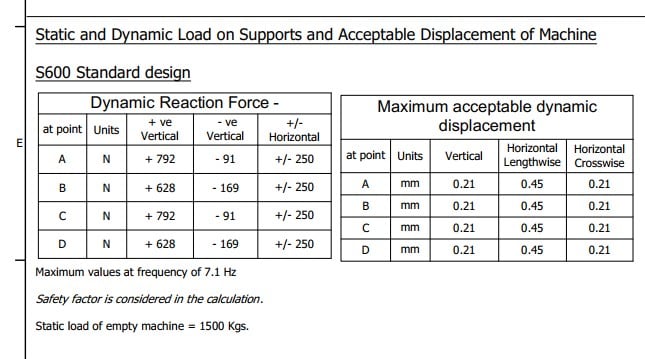
The problem is I have never applied dynamic forces in my software (SCIA) and I'm not well versed with dynamic design. Since the loads are very small (maximum vertically around 800 N, that's 80 kgf), would it be acceptable if I just multiply these values with a factor of 5 or something and use static design
