aniiben
Mechanical
- May 9, 2017
- 165
A part similar to the one shown ASME Y14.8-2009 Fig 4-9 (page 28). (Casting Standard)
The one and important difference is that there is an “as –cast” hole thru the part that is not used as a datum feature on the machined drawing.
On the machined drawing: Casting datums and machined datums are shown similar to the datum scheme above. The hole in question (again, as–cast hole/feature) is dimensioned and toleranced from the casting datums and ALSO from the machining datums.
Pos 0.8(MMC) Z, Y, X
Pos 0.25 A, B, C
Z, Y, X- casting datum targets
A, B, C machined datums
Some design/product engineers are seeing this as double dimensioning, others as illegal or redundant and others are just in agreement with this scheme.
The intent is to avoid the “as-cast” hole/feature to be out of “functional specification” before the part is used in the assembly. Since the hole is “as-cast” and does not get machined Z, Y X datum scheme is needed, but deformation of the part during the removal of the material has also been noticed.
I have no much experience with casting and plastic parts, but learning…..
On Tec-Ease I’ve seen a similar example, but again, no “as-cast” hole / feature dimensioned from the casting datums and also from the machined datums (except the initial datum targets that are shown and described /become on the drawing machined datums feature). See attachment for Tec-Ease example.
On Tec-Ease example, lets say Ø15 holes is "as-cast" and is also dimensioned WRT to Z, y and X in addition the the current position Ø 0.4 to A, B(M) and C(M) shown. How you you see it? Double dimensioning, illegal (per the standard), redundant, correct or other?
The one and important difference is that there is an “as –cast” hole thru the part that is not used as a datum feature on the machined drawing.
On the machined drawing: Casting datums and machined datums are shown similar to the datum scheme above. The hole in question (again, as–cast hole/feature) is dimensioned and toleranced from the casting datums and ALSO from the machining datums.
Pos 0.8(MMC) Z, Y, X
Pos 0.25 A, B, C
Z, Y, X- casting datum targets
A, B, C machined datums
Some design/product engineers are seeing this as double dimensioning, others as illegal or redundant and others are just in agreement with this scheme.
The intent is to avoid the “as-cast” hole/feature to be out of “functional specification” before the part is used in the assembly. Since the hole is “as-cast” and does not get machined Z, Y X datum scheme is needed, but deformation of the part during the removal of the material has also been noticed.
I have no much experience with casting and plastic parts, but learning…..
On Tec-Ease I’ve seen a similar example, but again, no “as-cast” hole / feature dimensioned from the casting datums and also from the machined datums (except the initial datum targets that are shown and described /become on the drawing machined datums feature). See attachment for Tec-Ease example.
On Tec-Ease example, lets say Ø15 holes is "as-cast" and is also dimensioned WRT to Z, y and X in addition the the current position Ø 0.4 to A, B(M) and C(M) shown. How you you see it? Double dimensioning, illegal (per the standard), redundant, correct or other?
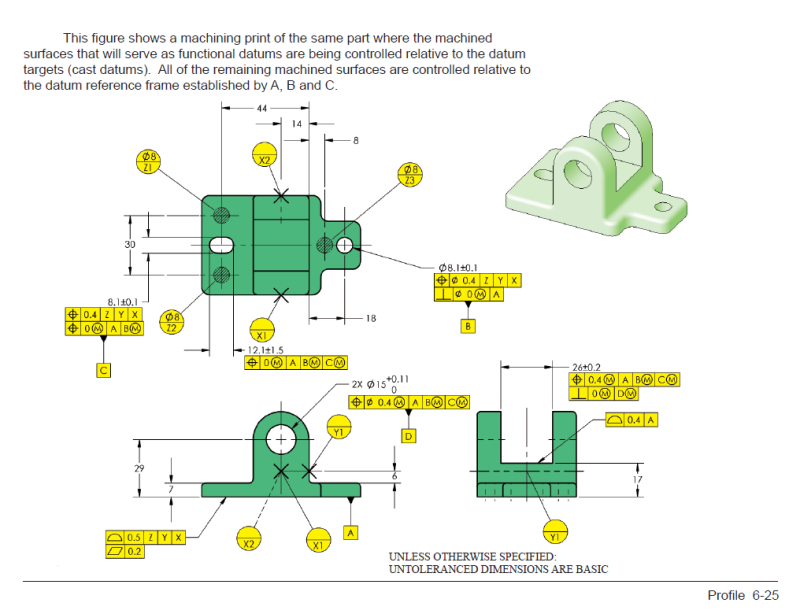