Hi!
I have been asked to add thermal breaks at steel outrigger members, where they connect to the base concrete structure as shown:
I have tried out Hilti Profis's calculation for plate with stand-off and would need to increase the bolt size to meet their criteria for bolt bending. I have also looked at some structural thermal break products and find that the modulus of elasticity is similar to that of steel. With this being the case, am I being too conservative by checking for this stand-off distance? Does anyone have thoughts on this or a recommended product from a similar experience?
Thanks so much!
I have been asked to add thermal breaks at steel outrigger members, where they connect to the base concrete structure as shown:
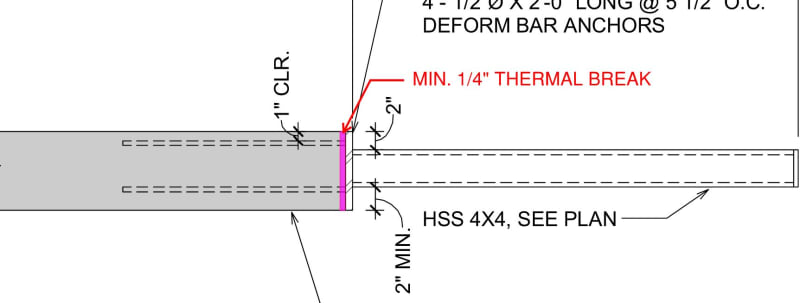
I have tried out Hilti Profis's calculation for plate with stand-off and would need to increase the bolt size to meet their criteria for bolt bending. I have also looked at some structural thermal break products and find that the modulus of elasticity is similar to that of steel. With this being the case, am I being too conservative by checking for this stand-off distance? Does anyone have thoughts on this or a recommended product from a similar experience?
Thanks so much!