OP:
"(please disregard that the holes are threaded... it's beside the point here)"
Everyone else:
disregards the written message and only addresses what they see in the picture.
OP, don't ever do that. If you attach a picture make sure that what's in that picture corresponds to the intent of your question without any terrible distractions.
The reason I asked to disregard that the hole are threaded is that
this picture is from a student homework in my gd&t class. I asked the studends to create a series of geometries on a part that would require different gd&t concepts: LMC, composite tolerances, multi-segments tolerances, profile of surface etc...
I am aware of the limits of usign LMC on a threaded hole, as it is not possible to gage such a feature. I am also aware that using profile of a surface with a non basic dimension makes no sense. As for the use of MMC on a threaded hole, I am also aware that threaded hole are self centering and have to added clearence once tightened. But not using MMC implies usign the actual mating enveloppe when inspecting (expendable thread gauge) which is expensive and rarelly (if ever) usefull.
But I was confronted by that scenario where a pattern of a hole is required to hold an other part in place with a somewhat larger tolerance, while maintaining the ability to assemble. usually, this is done with a composite tolerance. The added difficulty is that the hole is made on a thin sheet metal plate.
I was trying to figure out if composite tolerances is usefull in such a case, when
I think I realised that using composite with LMC is not usefull since the upper segment value is the positionnal error leading to barely enough material. This being said, what would the lower value be? I can't find any logical answer to that question. I wanted to confirm with the community of talented people on this forum that I did understand correctly.
In order to remove some of the confusion, I have modified the drawing removing the threads and added 3 scenarios of plausible way to dimension the part. Hopefully It will be less of a distraction.
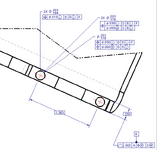