LiftDivergence
Aerospace
Hi all,
A few months ago I saw an post to the "Aircraft Structures" group on LinkedIn. I'm not going to link to to the post because I don't want to link to external sites in the forum. But this is a public group on LinkedIn with ~27,000 members where various aircraft structures are discussed, usually structural repairs.
The post in question was showing a repair for an aft fuselage skin belt loader impact on a circumferential splice. A large area of the skin was pretty severely dented and buckled in. They trimmed out a large area both skin panels across the splice. I have attached some pictures of the trimout and also the completed repair (external and internal).
What immediately struck me about the repair was their choice to design it as a "split patch". Effectively, one doubler for each skin panel with no continuity between them (other than the replaced production internal splice strap).
In my experience, I would have expected a repair for this damage would either have a continuous doubler over the splice, or a tripler layer over the split doublers. This comes both from familiarity with SRM repairs for several different makes/models of aircraft where a trimout is made on a skin splice, and from analysis experience of reinforcements spanning damage across splices.
There is some discussion on the post pointing this out. However, the individual who posted the repair seemed adamant that this was correct.
I'm curious what people think of the pros & cons of this design. I have my opinion of course, but I'm curious what other peoples experiences are.
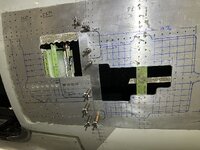
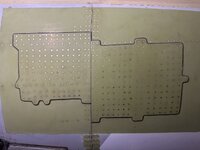
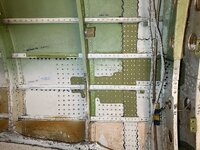
A few months ago I saw an post to the "Aircraft Structures" group on LinkedIn. I'm not going to link to to the post because I don't want to link to external sites in the forum. But this is a public group on LinkedIn with ~27,000 members where various aircraft structures are discussed, usually structural repairs.
The post in question was showing a repair for an aft fuselage skin belt loader impact on a circumferential splice. A large area of the skin was pretty severely dented and buckled in. They trimmed out a large area both skin panels across the splice. I have attached some pictures of the trimout and also the completed repair (external and internal).
What immediately struck me about the repair was their choice to design it as a "split patch". Effectively, one doubler for each skin panel with no continuity between them (other than the replaced production internal splice strap).
In my experience, I would have expected a repair for this damage would either have a continuous doubler over the splice, or a tripler layer over the split doublers. This comes both from familiarity with SRM repairs for several different makes/models of aircraft where a trimout is made on a skin splice, and from analysis experience of reinforcements spanning damage across splices.
There is some discussion on the post pointing this out. However, the individual who posted the repair seemed adamant that this was correct.
I'm curious what people think of the pros & cons of this design. I have my opinion of course, but I'm curious what other peoples experiences are.
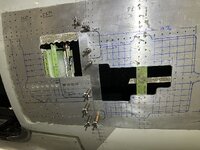
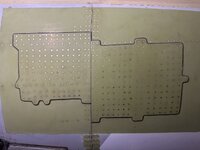
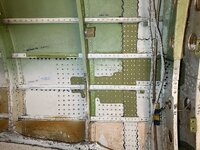