Hello everyone,
I watched the milling machine worker measuring the upper surface of the machined part while it was still on the milling machine.
He didn’t really pay attention to the dial indicator posture/position relative to the part and/or machine.
I wonder if there is no importance to the dial indicator posture/position.
I think that he should theoretically want to make the dial indicator “R” axis of rotation so he will be parallel to the milling machine FIXING BASE PLATE.
Any other position could lead to a projection of the real surface deviation.
What do you think?
I watched the milling machine worker measuring the upper surface of the machined part while it was still on the milling machine.
He didn’t really pay attention to the dial indicator posture/position relative to the part and/or machine.
I wonder if there is no importance to the dial indicator posture/position.
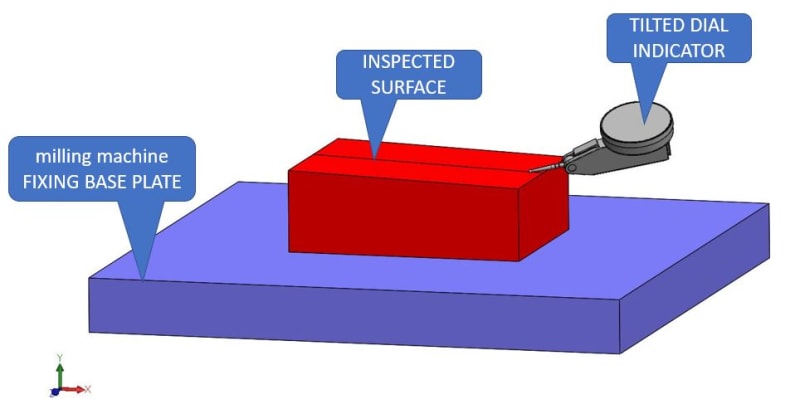
I think that he should theoretically want to make the dial indicator “R” axis of rotation so he will be parallel to the milling machine FIXING BASE PLATE.
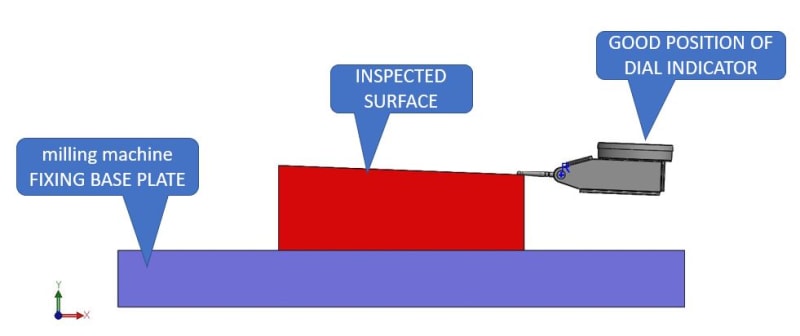
Any other position could lead to a projection of the real surface deviation.
What do you think?
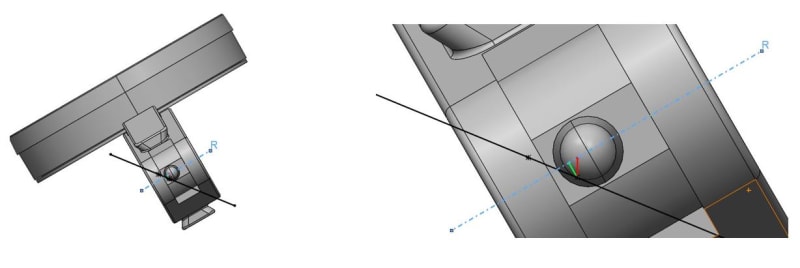