Our present 10 ton hoist motor is two speed two winding rated for 415V, 12/4 HP, 1440/465 RPM with electrically operated spring brake as shown below.
To reduce the high inrush current of about 80 Amps, I plan to rewind the motor for single speed 16 HP/25 Amp/1440 RPM and use a VFD.
The VFD will have two speed settings for 1500/600 RPM with pendant and as well radio controls. The exiting electrically operated brake will be retained.
The duty cycle max is 15 minutes ON (up and down continuous as well as inching) and 45 minutes OFF in an hour and the rewound motor will have ample thermal reserve.
What is the recommended VFD capacity for the hoist? 25 Amps or more?
Would a standard off the shelf VFD do or do I need one rated for hoist duty?
Muthu
To reduce the high inrush current of about 80 Amps, I plan to rewind the motor for single speed 16 HP/25 Amp/1440 RPM and use a VFD.
The VFD will have two speed settings for 1500/600 RPM with pendant and as well radio controls. The exiting electrically operated brake will be retained.
The duty cycle max is 15 minutes ON (up and down continuous as well as inching) and 45 minutes OFF in an hour and the rewound motor will have ample thermal reserve.
What is the recommended VFD capacity for the hoist? 25 Amps or more?
Would a standard off the shelf VFD do or do I need one rated for hoist duty?
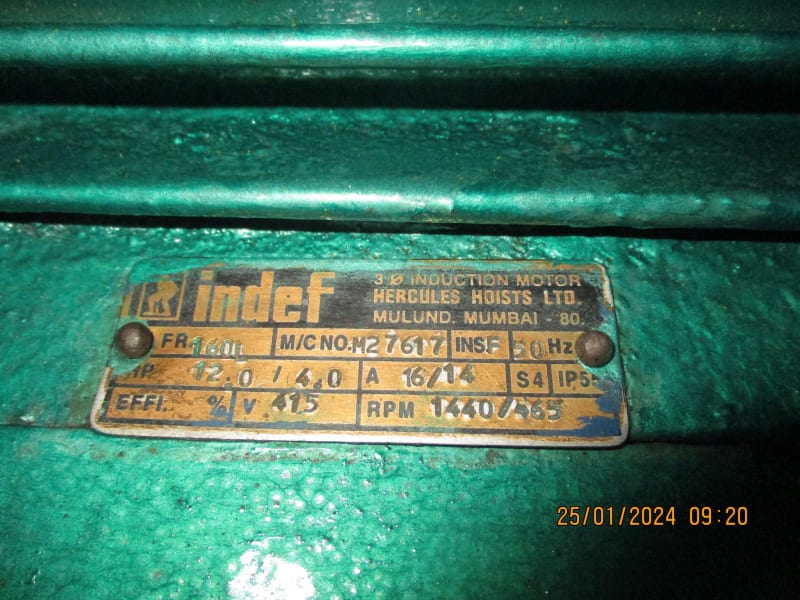
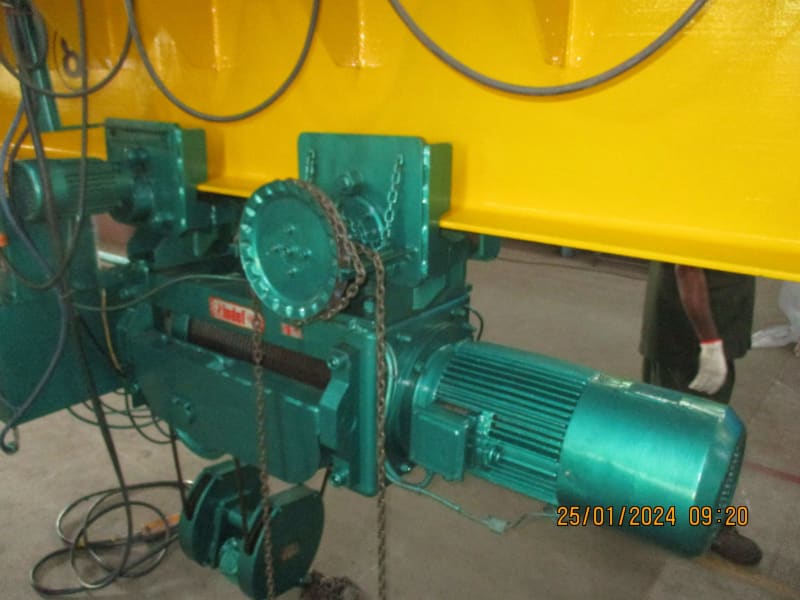
Muthu