Hi,
I tried to measure the current and voltage of an induction motor driven by a VSD. The measurement was taken at the input of the VSD, and the results are as follows:
Voltage:
Current:
The waveforms are heavily distorted, especially the current waveform. Is this normal? Could it be caused by harmonic distortion? Note that the voltage waveform also appears distorted even when the motor is not running.
Thanks,
Angga
I tried to measure the current and voltage of an induction motor driven by a VSD. The measurement was taken at the input of the VSD, and the results are as follows:
Voltage:
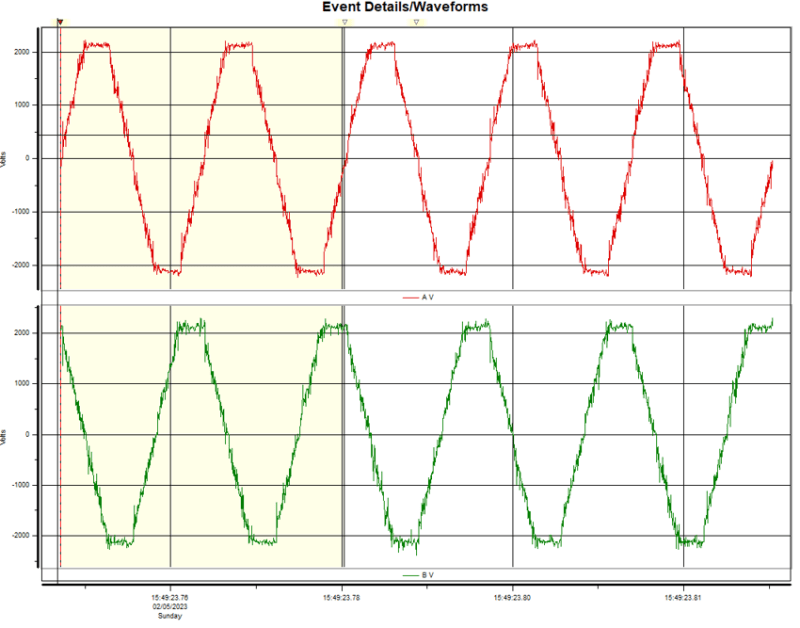
Current:
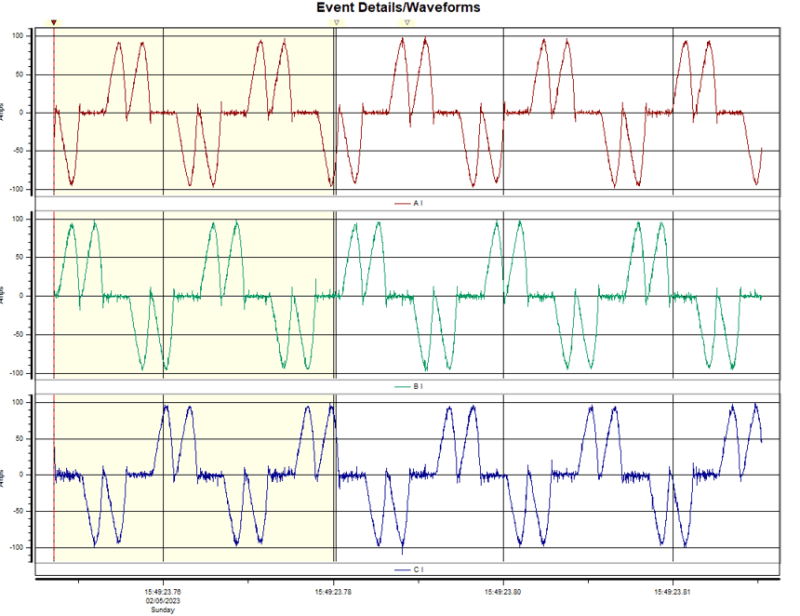
The waveforms are heavily distorted, especially the current waveform. Is this normal? Could it be caused by harmonic distortion? Note that the voltage waveform also appears distorted even when the motor is not running.
Thanks,
Angga