Hello,
In a MV MW system with a VFD driving a motor, how do you handle grounding the High Frequency common mode currents?
The rotor has shaft grounding which is grounded to the stator frame.
Stator frame is grounded via the PE cable routed in the same cable tray as the power cables. The PE cable is terminated at the noise source, the VFD.
In the Aegis HF grounding strap white paper attached, and in the picture below:
It is recommended to ground the stator frame, driven equipment and VFD using a HF grounding strap.
My question is:
Would the best return path for HF noise not be the cable tray well connected from stator frame to VFD + PE cable and a bare Cu cable.
Instead of grounding the HF noise to your foundation grounding, where you have no clue about the return path to the VFD creating possible signal cable interference?
I hope you have some insights on this, please reach out if i need to explain myself further.
Kind regards - Jens.
In a MV MW system with a VFD driving a motor, how do you handle grounding the High Frequency common mode currents?
The rotor has shaft grounding which is grounded to the stator frame.
Stator frame is grounded via the PE cable routed in the same cable tray as the power cables. The PE cable is terminated at the noise source, the VFD.
In the Aegis HF grounding strap white paper attached, and in the picture below:
It is recommended to ground the stator frame, driven equipment and VFD using a HF grounding strap.
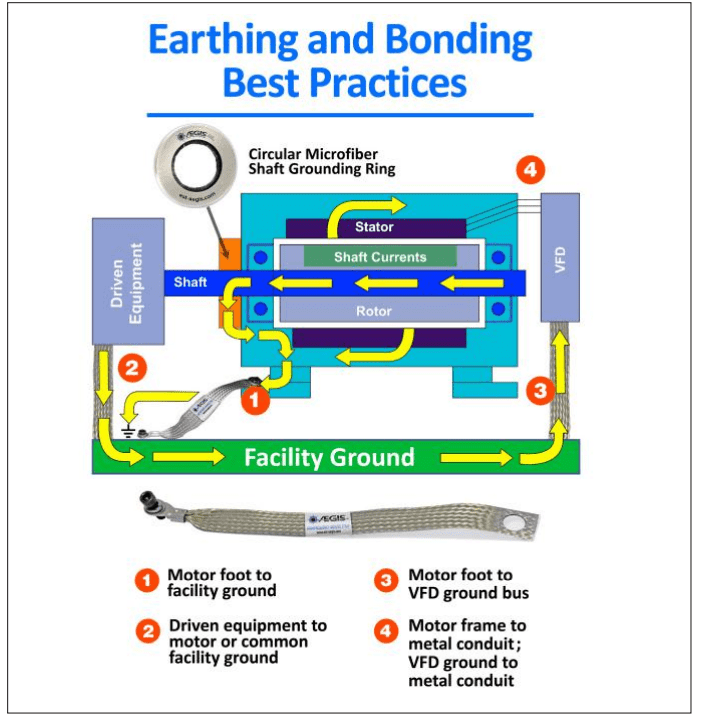
My question is:
Would the best return path for HF noise not be the cable tray well connected from stator frame to VFD + PE cable and a bare Cu cable.
Instead of grounding the HF noise to your foundation grounding, where you have no clue about the return path to the VFD creating possible signal cable interference?
I hope you have some insights on this, please reach out if i need to explain myself further.
Kind regards - Jens.