juanMElvl300
Mechanical
Hi users hope you are all doing good.
I have two simple questions.
1) is it ok to have a profile surface tolerance in a drawing title block? (see the below picture)
2) if so, with it apply to all surfaces for inspection?
I'm used to seeing the old way; this profile tolerance must be new. (to me btw)
something like this was the old tol. block
X.X = ±0.25
X.XX = ±0.12
X.XXX = ±0.06
X.XXXX = SEE DIM TOLERANCE
I have two simple questions.
1) is it ok to have a profile surface tolerance in a drawing title block? (see the below picture)
2) if so, with it apply to all surfaces for inspection?
I'm used to seeing the old way; this profile tolerance must be new. (to me btw)
something like this was the old tol. block
X.X = ±0.25
X.XX = ±0.12
X.XXX = ±0.06
X.XXXX = SEE DIM TOLERANCE
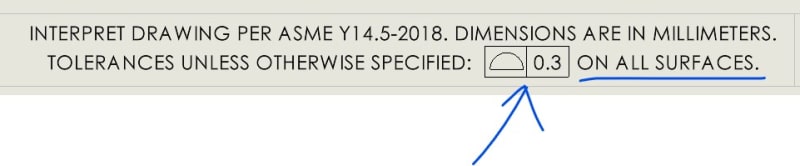