Hello,
I'am doing a Joule heating study of a simple cable model.
The cable has a terminal of 50A in one end, and a ground in the other end.
A heat flux is added to the surface.
My problem is:
I am simulating a Stranded cable as a solid cable in comsol for time saving and mesh optimisation.
This however makes it so that the solid cable in the simulation has more copper than the real life stranded cable using the same diameter.
I want to change the simulation so that i dictacte the resistivity from the standard 1.72 e-7 to a value of my choice.
Is there a way to do this? Or should i go with another aproach to manually decide the resistance of the cable?
Right now the linearized resistivity value isn't used by COMSOL. Unless i choose linearized resistivity in the constitutive relation.
But this makes the model take 10 years to compute.
Thanks in advance!
Kind regards - Jens
I'am doing a Joule heating study of a simple cable model.
The cable has a terminal of 50A in one end, and a ground in the other end.
A heat flux is added to the surface.
My problem is:
I am simulating a Stranded cable as a solid cable in comsol for time saving and mesh optimisation.
This however makes it so that the solid cable in the simulation has more copper than the real life stranded cable using the same diameter.
I want to change the simulation so that i dictacte the resistivity from the standard 1.72 e-7 to a value of my choice.
Is there a way to do this? Or should i go with another aproach to manually decide the resistance of the cable?
Right now the linearized resistivity value isn't used by COMSOL. Unless i choose linearized resistivity in the constitutive relation.
But this makes the model take 10 years to compute.
Thanks in advance!
Kind regards - Jens
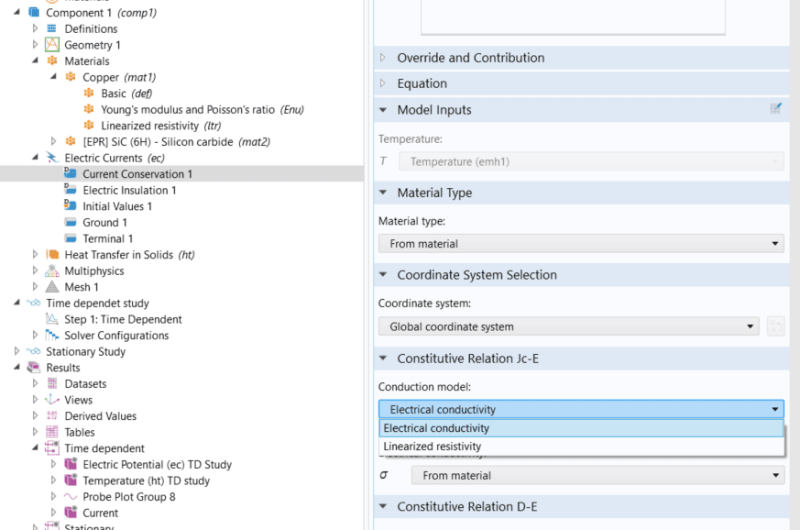
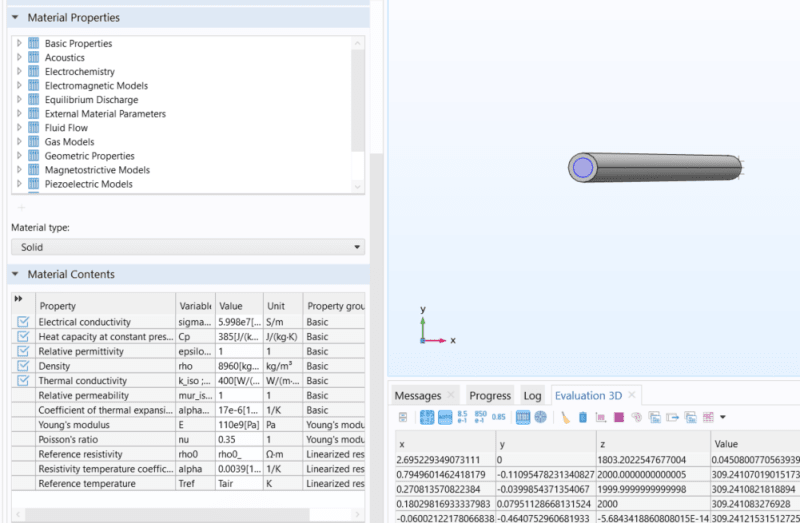