sendithard
Industrial
With rule #1 a feature of size must be in perfect form at MMC.
Where this confuses me is I thought if you apply MMC *with* positional tolerance then the hole can be out of perpendicularity up to the tol zone amount.
Am I thinking correctly whereby you would need a FCF with zero positional tolerance to be enforcing rule #1 on a part? If you instead apply the above FCF with .10 tolerance then at MMC the hole could be out of perfect form, no?
Thanks.
Where this confuses me is I thought if you apply MMC *with* positional tolerance then the hole can be out of perpendicularity up to the tol zone amount.
Am I thinking correctly whereby you would need a FCF with zero positional tolerance to be enforcing rule #1 on a part? If you instead apply the above FCF with .10 tolerance then at MMC the hole could be out of perfect form, no?
Thanks.
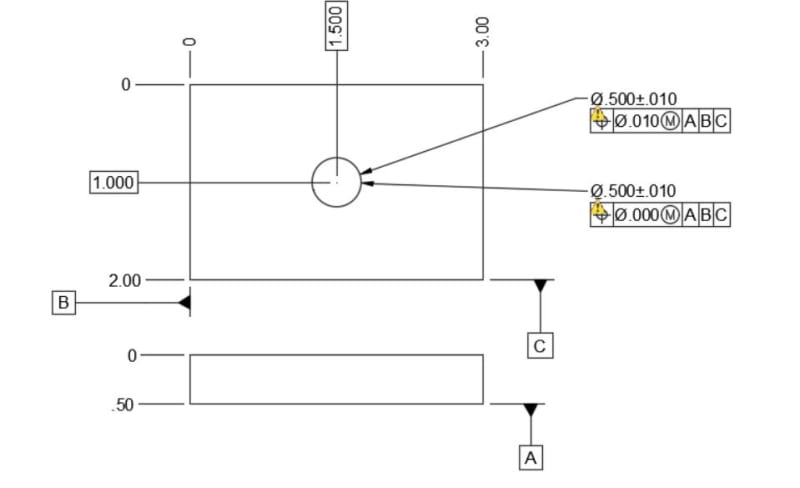