Redacted
Structural
- Mar 12, 2016
- 160
Good day, I need to reinforce a buttress at the top as it is damaged and there is also not enough shear capacity at the top to transfer the force to the lower portion of the buttress.
I would like to essentially jacket the existing buttress to increase the shear capacity and to transfer the force to the lower portion of the buttress. I do not want to jacket the entire column (plan to only go about 5' down from the top, the full height of the buttress is about 18'). I would just like to provide a jacket at the top to successfully transfer the force to the stronger part of the existing buttress.
I essentially would like to calculate how many dowels I need transfer this force.
I haven't done a concrete jacketing calculation before but have done shear stud designs for steel beams. I’m not sure if I am approaching this the right way so any help would be appreciated.
See shear flow calculations below :
I am not sure how to calculate the required confinement reinforcement either? Any help on that would be helpful.
I also need to replace about 2' of concrete at the top of the buttress with new concrete. To connect the new concrete to the old, would I need additional vertical bars doweled into the existing concrete? Would these vertical bars need to take the full shear force? If so I don't think it will work as it would need 27 bars in a 2'x2' space. Or would the top 2' of new concrete just act with the new confinement bars and dowels going down the buttress to transfer the load?
I am trying to also visualise how this detail would work, as it is not going all the way down to the foundation and as it is a buttress the section will get larger the farther down you go. I don't see much literature on strengthening of buttresses so I am treating this like a column, which should be a conservative approach, as the shear capacity should increase linearly down the buttress.
I would like to essentially jacket the existing buttress to increase the shear capacity and to transfer the force to the lower portion of the buttress. I do not want to jacket the entire column (plan to only go about 5' down from the top, the full height of the buttress is about 18'). I would just like to provide a jacket at the top to successfully transfer the force to the stronger part of the existing buttress.
I essentially would like to calculate how many dowels I need transfer this force.
I haven't done a concrete jacketing calculation before but have done shear stud designs for steel beams. I’m not sure if I am approaching this the right way so any help would be appreciated.
See shear flow calculations below :
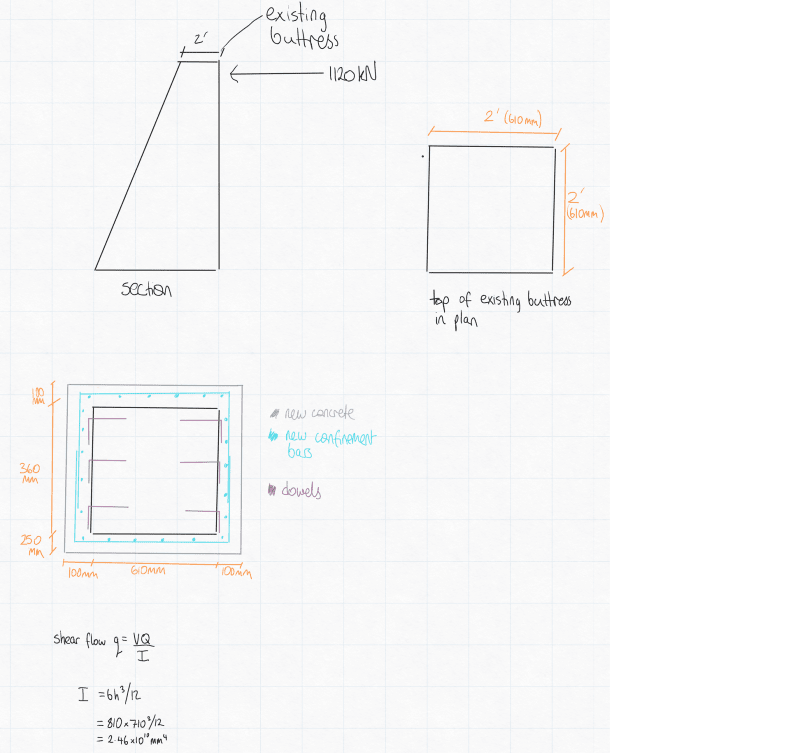
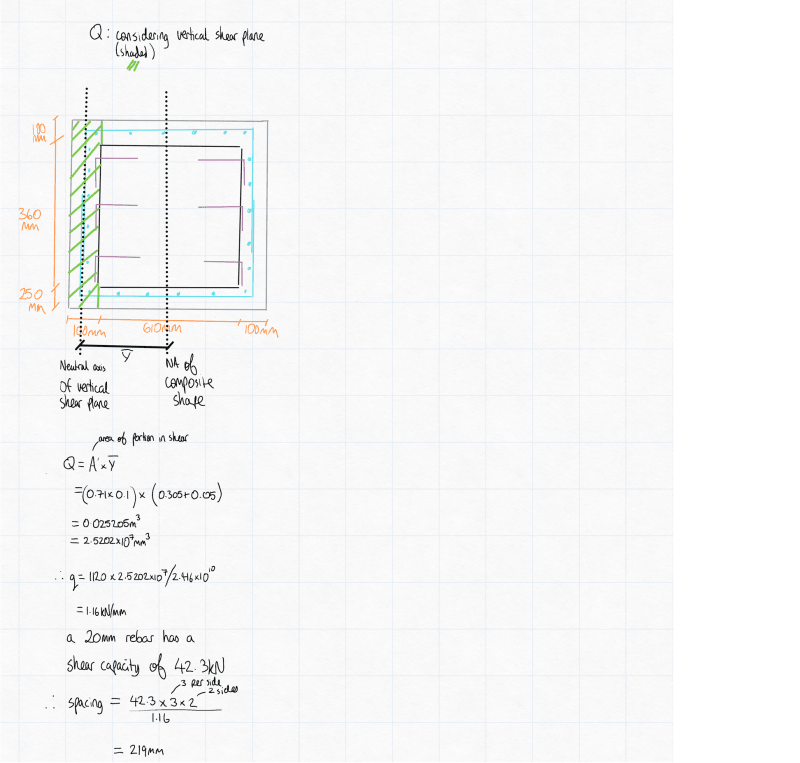
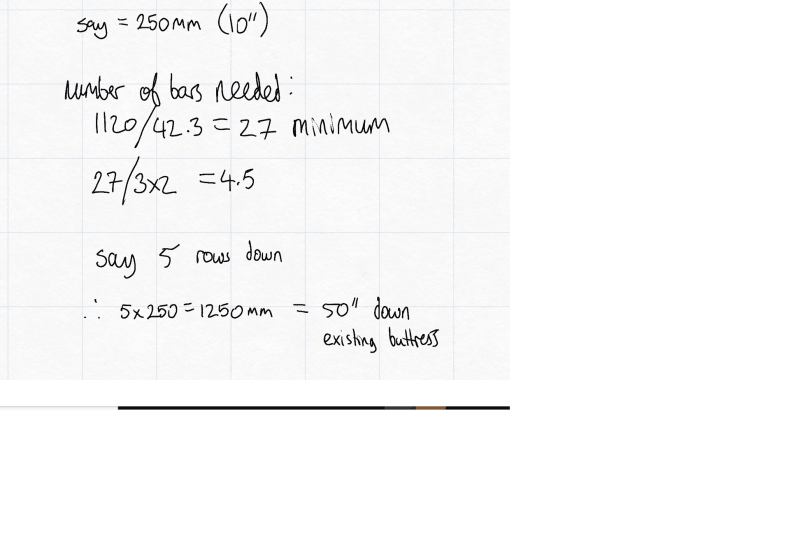
I am not sure how to calculate the required confinement reinforcement either? Any help on that would be helpful.
I also need to replace about 2' of concrete at the top of the buttress with new concrete. To connect the new concrete to the old, would I need additional vertical bars doweled into the existing concrete? Would these vertical bars need to take the full shear force? If so I don't think it will work as it would need 27 bars in a 2'x2' space. Or would the top 2' of new concrete just act with the new confinement bars and dowels going down the buttress to transfer the load?
I am trying to also visualise how this detail would work, as it is not going all the way down to the foundation and as it is a buttress the section will get larger the farther down you go. I don't see much literature on strengthening of buttresses so I am treating this like a column, which should be a conservative approach, as the shear capacity should increase linearly down the buttress.