We have inherited a die to stamp out a part which must be flat within 0.010". The part is mild steel at 0.125" thick. I've attached a sketch of the part with some dimensions which show various widths of the material and the proximity of the holes to the edge. The geometry appears to make it extremely difficult to maintain flatness due to the excessive stress that will build up during stamping. The die is not a fineblanking die or a Grip Flow die, but it is a cut and carry with pressure. The material is flat as it enters the die. So, a few questions...
1. Would you take the risk of assuring the flatness spec?
2. What would you do to help maintain flatness and/or regain flatness after stamping?
I appreciate the help.
1. Would you take the risk of assuring the flatness spec?
2. What would you do to help maintain flatness and/or regain flatness after stamping?
I appreciate the help.
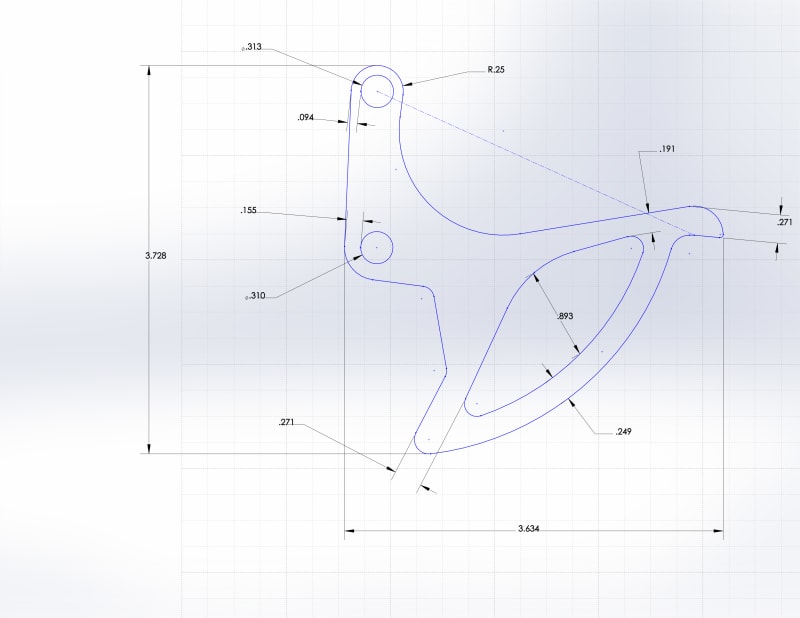