Hello Everyone I have been viewing this forum for a while now and this is my first post and I hope someone could help me with this.
I am simulating a wrap spring clutch/brake mechanism in which a shaft is placed inside a torsion spring with an interference fit between the spring's Inner Diameter and the shaft. When the shaft tries to rotate in the direction of winding a spring wraps around the shaft making the shaft impossible to move. But on the other hand if it rotates in the opposite direction the interference is released and the shaft moves freely.
I am simulating this mechanism in Abaqus Standard where I have two different steps and two interaction property. In the first step I have included the frictionless normal behavior with the interference feature on. In the next step I am inputting the friction that will be in the system and have included a moment load.
The problem that I am having is the shaft rotates but I am not able to see the contact pressure increase during rotation of the shaft can someone tell me why I am not able to visualize it?
I am simulating a wrap spring clutch/brake mechanism in which a shaft is placed inside a torsion spring with an interference fit between the spring's Inner Diameter and the shaft. When the shaft tries to rotate in the direction of winding a spring wraps around the shaft making the shaft impossible to move. But on the other hand if it rotates in the opposite direction the interference is released and the shaft moves freely.
I am simulating this mechanism in Abaqus Standard where I have two different steps and two interaction property. In the first step I have included the frictionless normal behavior with the interference feature on. In the next step I am inputting the friction that will be in the system and have included a moment load.
The problem that I am having is the shaft rotates but I am not able to see the contact pressure increase during rotation of the shaft can someone tell me why I am not able to visualize it?
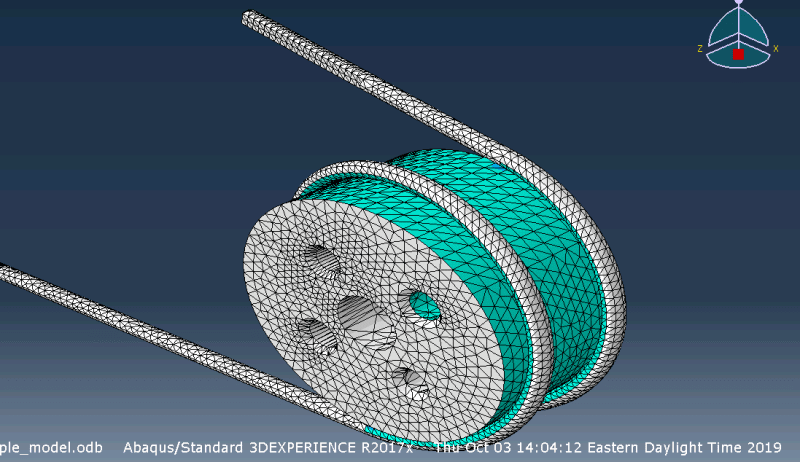
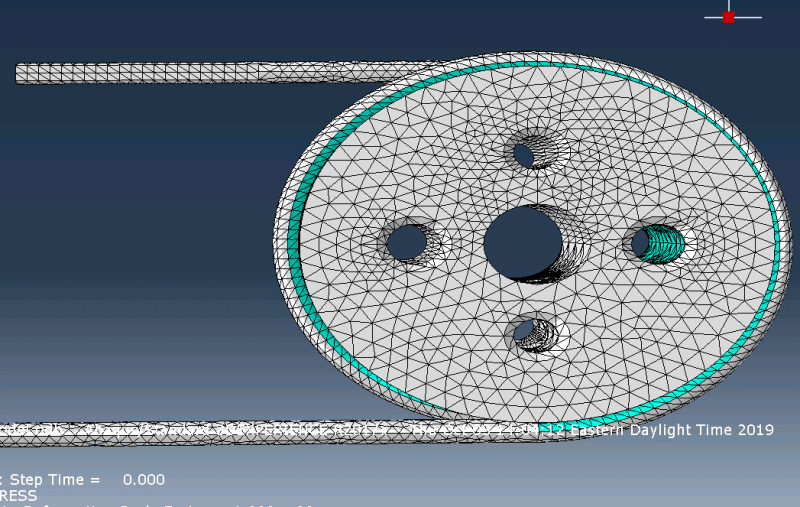
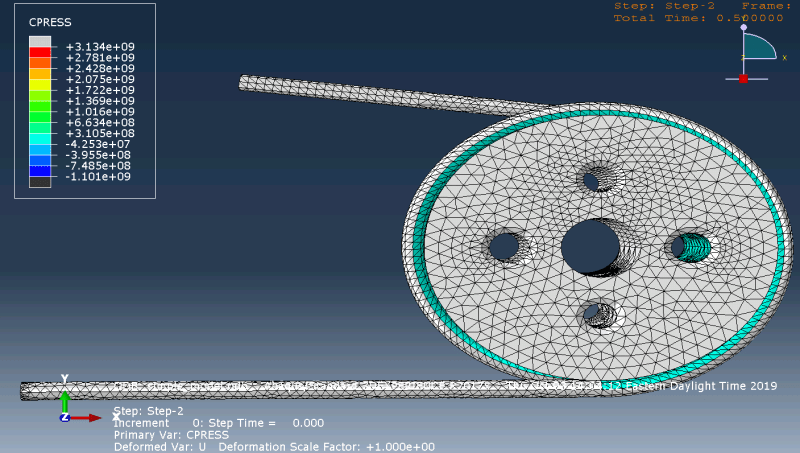