Background: A PQR test coupon with 10mm thick, welded by multi-process GTAW +SMAW ,the deposit metal thickness is 3mm and 7mm respectively.
QUESTION: (1)for cold band test, TWO FACE and TWO back bend specimen will be tested to represent GTAW and SMAW deposit metal.
(2)for impact test, as illustrated following
Does two sets of impact test specimen shall be test from GTAW and SMAW deposit metal it's HAZ respectively?
If yes,why? who can provide the reference code interpretation.
QUESTION: (1)for cold band test, TWO FACE and TWO back bend specimen will be tested to represent GTAW and SMAW deposit metal.
(2)for impact test, as illustrated following
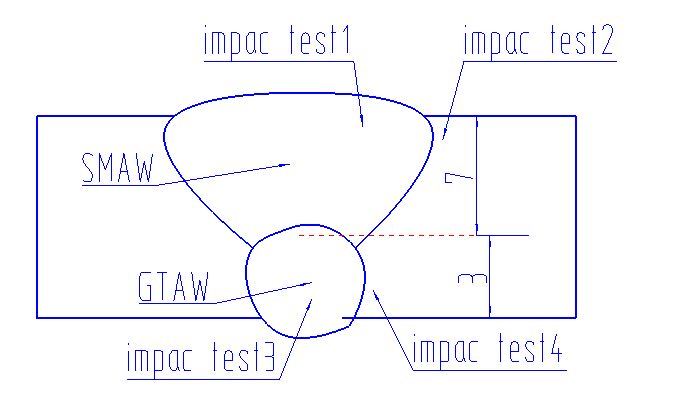
Does two sets of impact test specimen shall be test from GTAW and SMAW deposit metal it's HAZ respectively?
If yes,why? who can provide the reference code interpretation.