PrintScaffold
Mechanical
- Sep 8, 2006
- 453
Very impressive! Does anybody know which CAD did they use? Was it NX, CATIA, or something else?
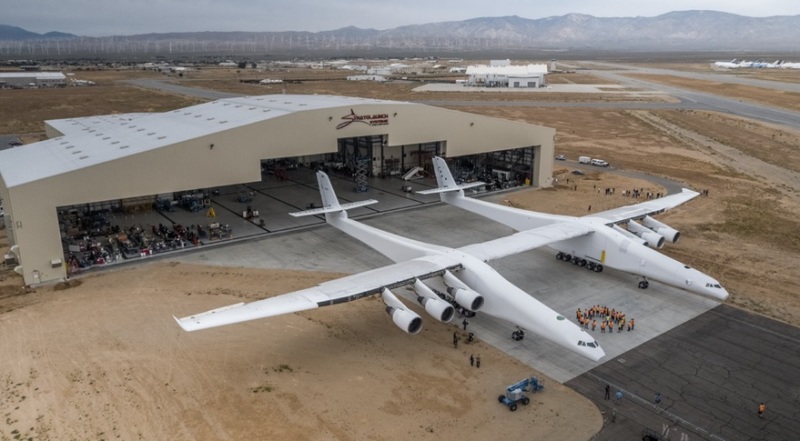
Follow along with the video below to see how to install our site as a web app on your home screen.
Note: This feature may not be available in some browsers.
TheTick said:The lack of elegance of curvature on the fuselage indicates SolidWorks.