mike b
Mechanical
- Aug 22, 2019
- 4
Im needing help with developing some calculations for bending and shear stress. The weld will consist of a partial bevel and a fillet (fillet #2) which joins a piece of flat bar to a piece of pipe. See the picture. This will be used for a bolt-on pressure retaining clamp. Our current calculation method is shown below but I believe it is very conservative. Thanks in advance.
Shear stress = Force / (length of weld) x (Fillet size)
Bending stress = [3 X Force X (pipe wall thickness)] / (Length of weld) X (weld thickness)
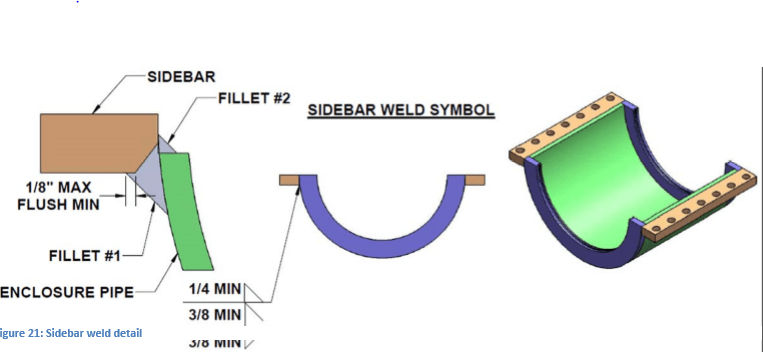
Shear stress = Force / (length of weld) x (Fillet size)
Bending stress = [3 X Force X (pipe wall thickness)] / (Length of weld) X (weld thickness)