delagina
Structural
- Sep 18, 2010
- 1,008
I have an I beam skid on slab. The I beam already has holes on bottom flange.
Can they drill into concrete if the I beam is just 12" high?
The top flange could be interfering with the drilling tool.
Of course they can remove the I beam skid and drill after they marked the location but can contractor drill with the skid on there?
I don't know all drilling tools out there and the clearance they require.
Can they drill into concrete if the I beam is just 12" high?
The top flange could be interfering with the drilling tool.
Of course they can remove the I beam skid and drill after they marked the location but can contractor drill with the skid on there?
I don't know all drilling tools out there and the clearance they require.
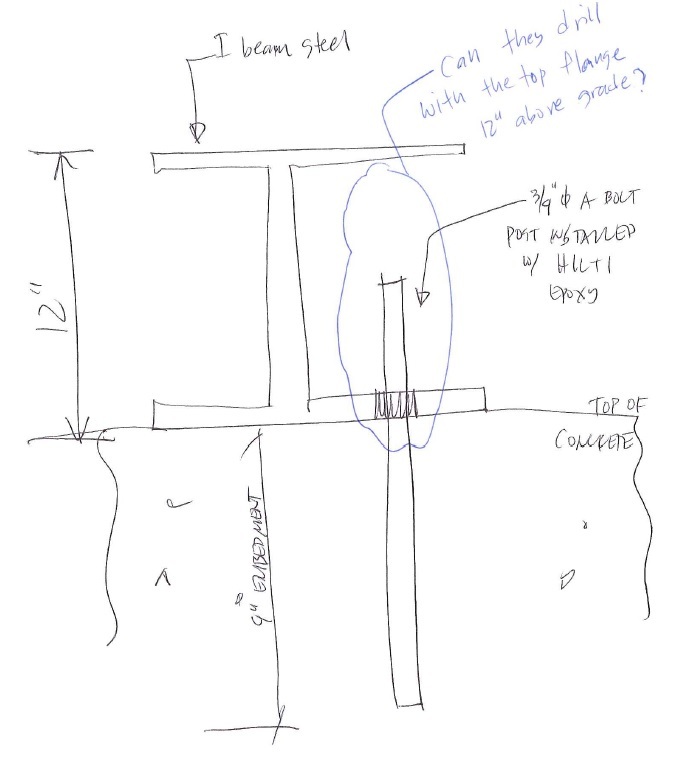