Hi everyone,
I'm trying to confirm my understanding of how to use spring loaded pressure regulators in parallel. My understanding of how to use regulators in parallel simultaneously, to deliver a flow rate that can't be achieved by one regulator alone, is shown in configuration B. My understanding as to why configuration A is not recommended is that having both regulators at the same set point would cause the regulators to interfere with each other. Configuration B would be setup such that the regulator at 30 psig would provide, say 1/3 of the total flow, and the regulator at 28 psig would provide the remaining 2/3s when the 30 psig regulator started to operate further into the droop as the flow demand increased. For configuration B, the two different setpoints would still meet the downstream pressure requirements of the bioreactors.
Edit: The flow demands I am trying to meet break down to typical and peak flow demands. Normally one regulator would be sufficient for the typical load, but a peak load scenario is now introduced where the flow demand is much higher. To resolve this, configuration A proposes two identical regulators working simultaneously to meet the flow demand downstream whether it is the typical or peak load. Configuration B, in my mind, basically dedicates the higher setpoint regulator to the typical load and the lower setpoint regulator to the peak load. In both cases, the droop from the higher flow scenarios would be looked at to ensure it was acceptable.
Do you agree with my assessment or have I missed something?
I'm trying to confirm my understanding of how to use spring loaded pressure regulators in parallel. My understanding of how to use regulators in parallel simultaneously, to deliver a flow rate that can't be achieved by one regulator alone, is shown in configuration B. My understanding as to why configuration A is not recommended is that having both regulators at the same set point would cause the regulators to interfere with each other. Configuration B would be setup such that the regulator at 30 psig would provide, say 1/3 of the total flow, and the regulator at 28 psig would provide the remaining 2/3s when the 30 psig regulator started to operate further into the droop as the flow demand increased. For configuration B, the two different setpoints would still meet the downstream pressure requirements of the bioreactors.
Edit: The flow demands I am trying to meet break down to typical and peak flow demands. Normally one regulator would be sufficient for the typical load, but a peak load scenario is now introduced where the flow demand is much higher. To resolve this, configuration A proposes two identical regulators working simultaneously to meet the flow demand downstream whether it is the typical or peak load. Configuration B, in my mind, basically dedicates the higher setpoint regulator to the typical load and the lower setpoint regulator to the peak load. In both cases, the droop from the higher flow scenarios would be looked at to ensure it was acceptable.
Do you agree with my assessment or have I missed something?
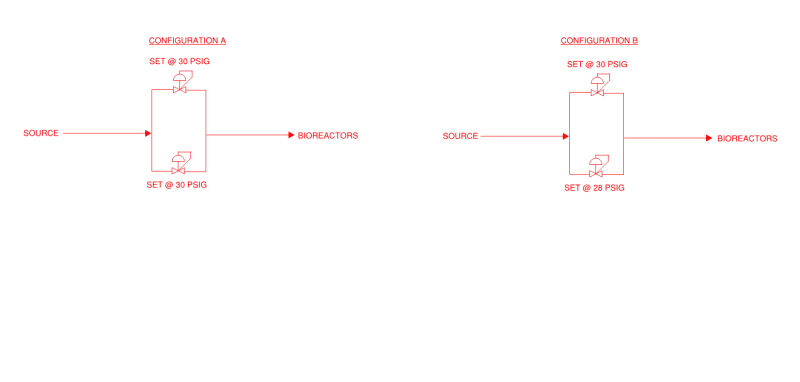