I'm working on a large machine that has an oil heated drum that runs partially submerged in tar.
This is essentially what it looks like and how it's currently built.
Dimensions are not exact and are in feet. (About 8 feet long)
As depicted they pump 250F° oil into the center pipe.
The pipe has a few hole pairs drilled 180° apart on the center in-feed pipe.
The oil leaves the drum out the end as shown.
Looking at this I think it really can't work very well because of the lack of pressure control on the oil, poor flow rate control, and probably lousy flow sharing by all the holes.
They've dissembled the drum looking for clogs or gunk and there has not been any.
They are complaining that the surface temperature of the tar soaked surface is all over the place varying by more than 70F° in various poorly defined regions. This is causing the laminating process to be.... sub par..
Is there a more modern standard way to be doing this that provides a modicum of uniformity? Maybe a single eductor at the end of the in-feed pipe? Or ?
Keith Cress
kcress -
This is essentially what it looks like and how it's currently built.
Dimensions are not exact and are in feet. (About 8 feet long)
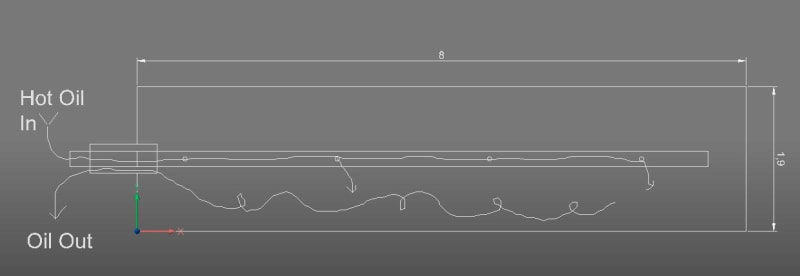
As depicted they pump 250F° oil into the center pipe.
The pipe has a few hole pairs drilled 180° apart on the center in-feed pipe.
The oil leaves the drum out the end as shown.
Looking at this I think it really can't work very well because of the lack of pressure control on the oil, poor flow rate control, and probably lousy flow sharing by all the holes.
They've dissembled the drum looking for clogs or gunk and there has not been any.
They are complaining that the surface temperature of the tar soaked surface is all over the place varying by more than 70F° in various poorly defined regions. This is causing the laminating process to be.... sub par..
Is there a more modern standard way to be doing this that provides a modicum of uniformity? Maybe a single eductor at the end of the in-feed pipe? Or ?
Keith Cress
kcress -