Hello
I'm performing transient heat transfer analysis and since i've never done it before I have encountered some problems. The task is to compare the results made in FEA software to an experiment. I have a low carbon steel plate ( 0.2x0.1x0.01 m dimensions ) which is excited by a laser on a top surface ( 30 Watts in 0.1s , laser spot radius = 0.0045m ) and then thermal imaging camera aquires image.
Then Im doing analysis in MSC Marc software.
Here's data :
Model units : m
MATERIAL PROPERTIES :
Thermal conductivity = 54 W/m*C
Specific heat = 465 J/kg*C
Density = 7863 kg/m^3
Intial temperature = 23.7586 C
Heat flux = 30W / Area , where Area = pi * 0.0045^2 which gives 471570 W/m^2
Surface heat flux = 471570 * exp(-((time-0.95)^2)/0.01) - assuming gauss distribution function
Natural convection coefficient = 10 W/m^2*C
Ambient temperature = 23 C
Film applied on whole top and bottom surface
Analysis type transient with 200 increments, which gives constant time step 0.008s , total time 1.6s
Finally , im comparing the temperatures 5 mm away from the heat source and here's what i get :
I've expected the result to be different, but not that much....
I'd be very grateful if someone could verify input data / units and provide me guidance what could be wrong here.
Regards
Mike
I'm performing transient heat transfer analysis and since i've never done it before I have encountered some problems. The task is to compare the results made in FEA software to an experiment. I have a low carbon steel plate ( 0.2x0.1x0.01 m dimensions ) which is excited by a laser on a top surface ( 30 Watts in 0.1s , laser spot radius = 0.0045m ) and then thermal imaging camera aquires image.

Then Im doing analysis in MSC Marc software.
Here's data :
Model units : m
MATERIAL PROPERTIES :
Thermal conductivity = 54 W/m*C
Specific heat = 465 J/kg*C
Density = 7863 kg/m^3
Intial temperature = 23.7586 C
Heat flux = 30W / Area , where Area = pi * 0.0045^2 which gives 471570 W/m^2
Surface heat flux = 471570 * exp(-((time-0.95)^2)/0.01) - assuming gauss distribution function
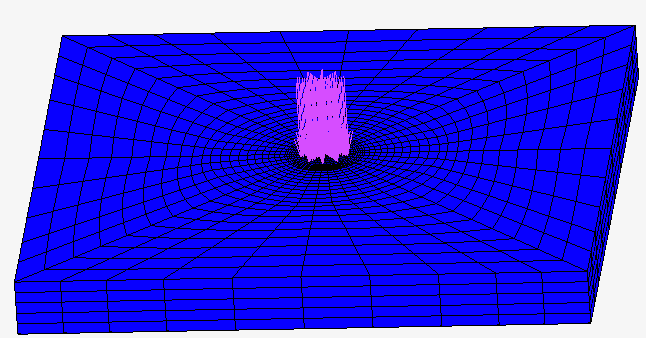
Natural convection coefficient = 10 W/m^2*C
Ambient temperature = 23 C
Film applied on whole top and bottom surface
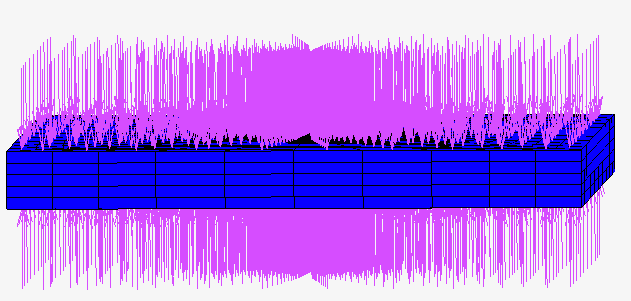
Analysis type transient with 200 increments, which gives constant time step 0.008s , total time 1.6s
Finally , im comparing the temperatures 5 mm away from the heat source and here's what i get :
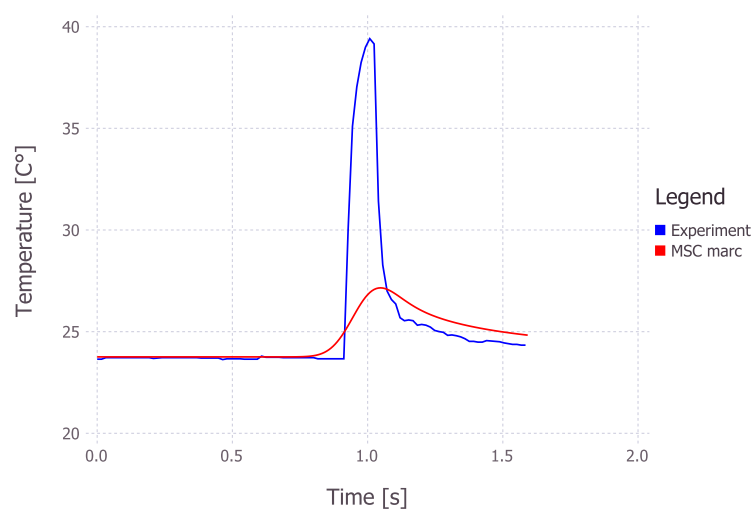
I've expected the result to be different, but not that much....
I'd be very grateful if someone could verify input data / units and provide me guidance what could be wrong here.
Regards
Mike