DisplayName001
Structural
- May 10, 2021
- 9
Hi I have questions about transfer structure design. Below is two RC transfer scenarios I have and wondering which one is better and one?
The left hand one I will check the punching shear, which I believe it is critical.
For the right hand one is there anything else that I need to look into in addition to punching shear?
Last question, is there any requirement in regards to the min. slab thickness for the purpose of starter bars for columns below and above?
Thank you
The left hand one I will check the punching shear, which I believe it is critical.
For the right hand one is there anything else that I need to look into in addition to punching shear?
Last question, is there any requirement in regards to the min. slab thickness for the purpose of starter bars for columns below and above?
Thank you
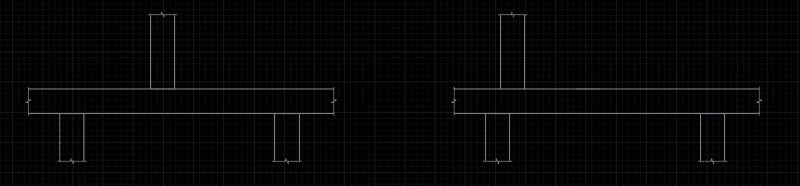